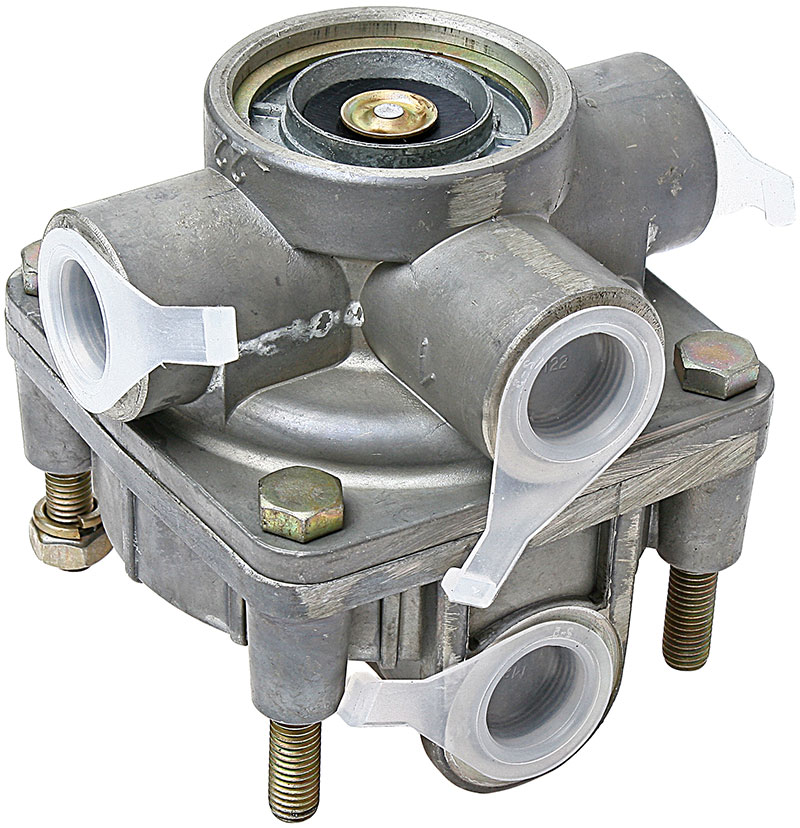
The pneumatic actuator of the brake system is simple and efficient in operation, however, the long length of the lines can lead to a delay in the operation of the brake mechanisms of the rear axles. This problem is solved by a special unit - an accelerator valve, the device and operation of which is devoted to this article.
What is an accelerator valve?
The accelerator valve (MC) is the control component of the brake system with a pneumatic drive. A valve assembly that distributes compressed air flows between the elements of the pneumatic system in accordance with the operating modes of the brakes.
The Criminal Code has two functions:
• Reduction of the response time of the brake wheel mechanisms of the rear axles;
• Improving the efficiency of parking and spare braking systems.
These units are equipped with trucks and buses, less often this unit is used on trailers and semi-trailers.
Types of accelerator valves
The management company can be divided into types according to applicability, method of management and configuration.
According to the applicability of the Criminal Code, there are two types:
- To control the contours of the parking (manual) and spare brakes;
- To control the elements of the pneumatic actuator of the actuators of the main brake system of the rear axles.
Most often, accelerator valves are included in the parking and spare brake systems, the actuators of which are energy accumulators (EA) combined with brake chambers. The unit controls the EA pneumatic circuit, providing rapid bleed of air during braking and its rapid supply from a separate air cylinder when removed from the brakes.
Accelerator valves are used much less frequently to control the main brakes. In this case, the unit carries out a rapid supply of compressed air from a separate air cylinder to the brake chambers during braking and bleed air during braking.
According to the method of management, the Criminal Code is divided into two large groups:
• Pneumatically controlled;
• Electronically controlled.
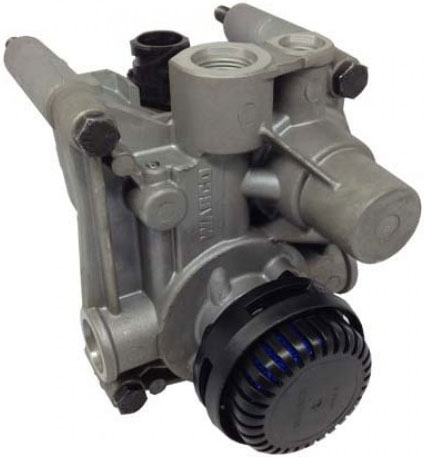
Electronically controlled accelerator
Pneumatically controlled valves are the simplest and most widely used. They are controlled by changing the pressure of the air coming from the main or manual brake valves. Electronically controlled valves contain solenoid valves, the operation of which is controlled by an electronic unit. Such management companies are used in vehicles with various automatic security systems (EBS and others).
According to the configuration, the Criminal Code is also divided into two groups:
• Without additional components;
• With the possibility of installing a muffler.
In the management company of the second type, a mount is provided for the installation of a muffler - a special device that reduces the noise intensity of the bleed air. However, the performance of both types of valves is the same.
Design and principle of operation of accelerator valves
The most simple is the design and functioning of the management company for the service brake system. It is based on a metal case with three pipes, inside of which there is a piston and the associated exhaust and bypass valves. Let's take a closer look at the design and operation of this type of management company using the example of the universal model 16.3518010.
The unit is connected as follows: pin I - to the control line of the pneumatic system (from the main brake valve), pin II - to the receiver, pin III - to the brake line (to the chambers). The valve works simply. During the movement of the vehicle, low pressure is observed in the control line, so the piston 1 is raised, the exhaust valve 2 is open and the brake line through the terminal III and channel 7 is connected to the atmosphere, the brakes are disinhibited. When braking, the pressure in the control line and in the chamber "A" increases, the piston 1 moves downwards, the valve 2 comes into contact with the seat 3 and pushes the bypass valve 4, which causes it to move away from the seat 5. As a result, pin II is connected to the chamber "B" and pin III - the air from the receiver is directed to the brake chambers, the car is braked. When disinhibiting, the pressure in the control line drops and the events described above are observed - the brake line is connected to channel 7 through pin III and the air from the brake chambers is discharged into the atmosphere, the vehicle is disinhibited.
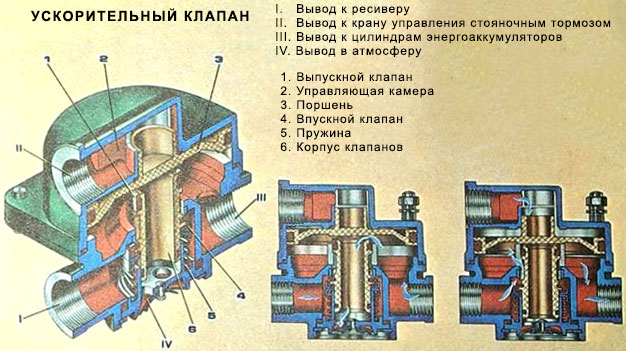
The device of the KAMAZ accelerator valve
The bellows-type hand pump works simply. Compression of the body by hand leads to an increase in pressure - under the influence of this pressure, the exhaust valve opens (and the intake valve remains closed), the air or fuel inside is pushed into the line. Then the body, due to its elasticity, returns to its original shape (expands), the pressure in it drops and becomes lower than atmospheric, the exhaust valve closes, and the intake valve opens. Fuel enters the pump through the open intake valve, and the next time the body is pressed, the cycle repeats.
The management company, designed for the "handbrake" and spare brake, is arranged similarly, but it is not controlled by the main brake valve, but by a manual brake valve ("handbrake"). Let's consider the principle of operation of this unit on the example of the corresponding unit of KAMAZ vehicles. Its terminal I is connected to the EA line of the rear brakes, the terminal II is connected to the atmosphere, the terminal III is connected to the receiver, the terminal IV is connected to the line of the hand brake valve. While the car is moving, high-pressure air is supplied to pins III and IV (from one receiver, so the pressure is the same here), but the area of the upper surface of the piston 3 is larger than the lower one, so it is in the lower position. The exhaust valve 1 is closed, and the intake valve 4 is open, the terminals I and III are communicated through the chamber "A", and the atmospheric outlet II is closed - compressed air is supplied to the EA, their springs are compressed and the system is disinhibited.
When the vehicle is put on the parking brake or when the spare brake system is activated, the pressure at the IV terminal decreases (the air is bleed off by a hand valve), the piston 3 rises, the exhaust valve opens, and the intake valve, on the contrary, closes. This leads to the connection of terminals I and II and the separation of terminals I and III - the air from the EA is vented into the atmosphere, the springs in them are unclenched and lead to braking of the vehicle. When removed from the handbrake, the processes proceed in reverse order.
Electronically controlled management companies can operate in the same way as described above, or be controlled by an electronic unit in accordance with the laid down algorithms. But in general, they solve the same problems as pneumatically controlled valves.
As you can see, the accelerator valve performs the functions of a relay - it controls the components of the pneumatic system remote from the main brake valve or manual valve, preventing pressure losses in long lines. This is what ensures fast and reliable operation of the brakes on the rear axles of the car.
Issues of selection and repair of the accelerator valve
During the operation of the car, the management company, like other components of the pneumatic system, is subjected to significant loads, so it should be periodically inspected for damage, air leaks, etc.
When replacing, it is necessary to install units of those types and models that are recommended by the automaker. If a decision is made to install analogues of the original valve, then the new unit must correspond to the original characteristics and installation dimensions. With other characteristics, the valve may not work correctly and not ensure the effective functioning of the brake system.
With the right choice of accelerator valve and timely maintenance, the brake system of a car or bus will work reliably, providing the necessary comfort and safety.
Post time: Aug-21-2023