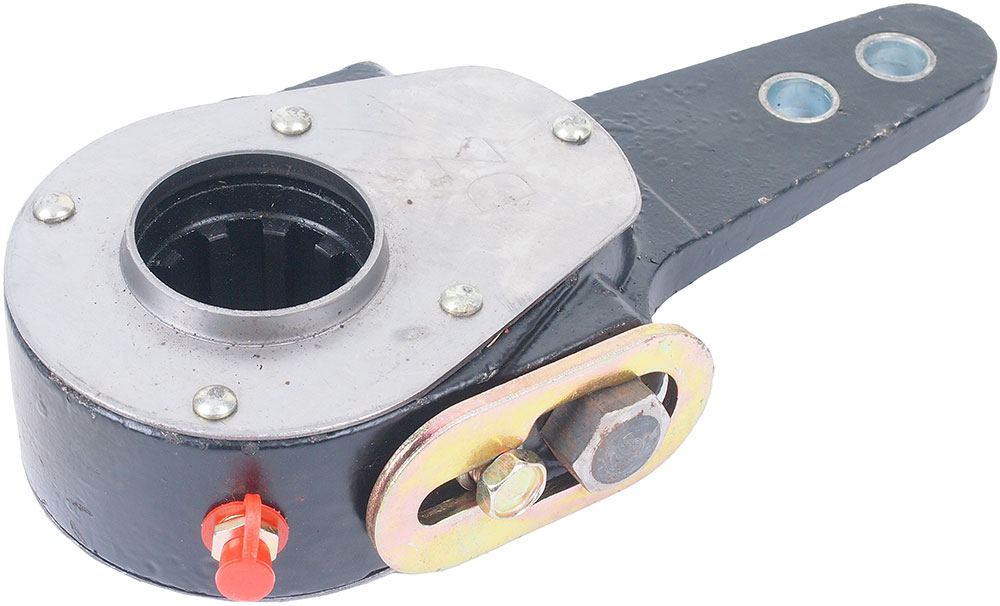
In cars, buses and other equipment with pneumatically operated brakes, the transfer of force from the brake chamber to the pads is carried out by means of a special part - an adjusting lever. Read all about levers, their types, design and applicability, as well as their selection and replacement, read the article.
What is an adjustment brake lever?
Adjusting brake lever ("ratchet") - a unit of wheel brakes of vehicles equipped with a pneumatically operated braking system; A device for transferring torque from the brake chamber to the brake pad drive and adjusting (manual or automatic) the working gap between the friction linings of the pads and the surface of the brake drum by changing the angle of the expansion knuckle.
Most modern heavy wheeled vehicles and various automotive equipment are equipped with a pneumatically operated brake system. The drive of mechanisms mounted on wheels in such a system is carried out with the help of brake chambers (TC), the stroke of the rod of which cannot change or changes within very narrow limits. This can lead to poor brake performance when the brake pads are worn out - at some point, the rod travel will no longer be enough to select the increased distance between the lining and the drum surface, and braking simply will not occur. To solve this problem, an additional unit is introduced into the wheel brakes to change and maintain the gap between the surfaces of these parts - the brake adjustment lever.
The adjusting lever has several functions:
● Mechanical connection of the TC and the expansion knuckle in order to transfer force to the pads to perform braking;
● Manual or automatic maintenance of the required distance between the friction linings and the working surface of the brake drum within the established limits (selection of the gap with gradual wear of the linings);
● Manual clearance adjustment when installing new friction linings or drum, after prolonged braking when driving downhill and in other situations.
Thanks to the lever, the necessary gap between the pads and the drum is maintained, which eliminates the need to adjust the stroke of the brake chamber rod and interfere with other parts of the brake mechanisms. This unit plays a very important role in ensuring the normal performance of the braking system and, as a result, the safety of the vehicle. Therefore, if the lever malfunctions, it must be replaced, but before making a purchase of a new part, you should understand the design, principle of operation and features of the adjusting levers.
Types, design and principle of operation of the adjusting brake lever
Two types of adjustment levers are used on vehicles:
● With manual regulator;
● With automatic regulator.
The simplest design is the levers with a manual regulator, which are more common on cars and buses of the early years of production. The basis of this part is a steel body in the form of a lever with an extension at the bottom. The lever has one or more holes for attaching a brake chamber to the fork. There is a large hole in the expansion for installing a worm gear with internal slots, a worm with an axis is perpendicular to the lever body. The axis of the worm on one side comes out of the body, on its outer end there is a turnkey hexagon. The axle is fixed from turning by a locking plate, which is held by a bolt. Additionally, a ball spring lock can be located in the lever - it provides fixation of the axis due to the emphasis of the steel ball in the spherical recesses on the axis. The downforce of the ball can be adjusted by a threaded stopper. The installation place of the gear pair of slot-gear and worm is closed on both sides with metal covers on rivets. On the outer surface of the housing there is also a grease fitting for supplying lubricant to the gear and a safety valve for the release of excessive amounts of grease.
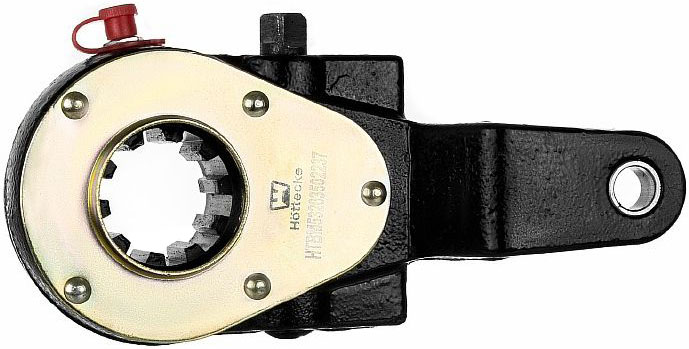
Adjustment lever with manual adjustment
The auto-adjusting lever has a more complex device. In such a lever there are additional parts - a ratchet cam mechanism, as well as movable and fixed couplings connected to the worm axis, which are driven by a pusher from a leash located on the side surface of the body.
The lever with an automatic regulator works as follows. With a normal gap between the pads and the drum, the lever functions in the same way as described above - it simply transfers the force from the brake chamber fork to the expansion knuckle. As the pads wear out, the lever rotates at a greater angle, this is tracked by a leash rigidly fixed to the bracket. In case of excessive wear of the linings, the leash rotates at a considerable angle and turns the movable clutch through the pusher. This, in turn, leads to the rotation of the ratchet mechanism by one step and the corresponding rotation of the worm axis - as a result, the spline gear and the expansion knuckle axis connected to it rotate, and the gap between the pads and the drum decreases. If a one-step turn is not enough, then during the next braking, the described processes will continue until the excessive clearance is fully sampled.
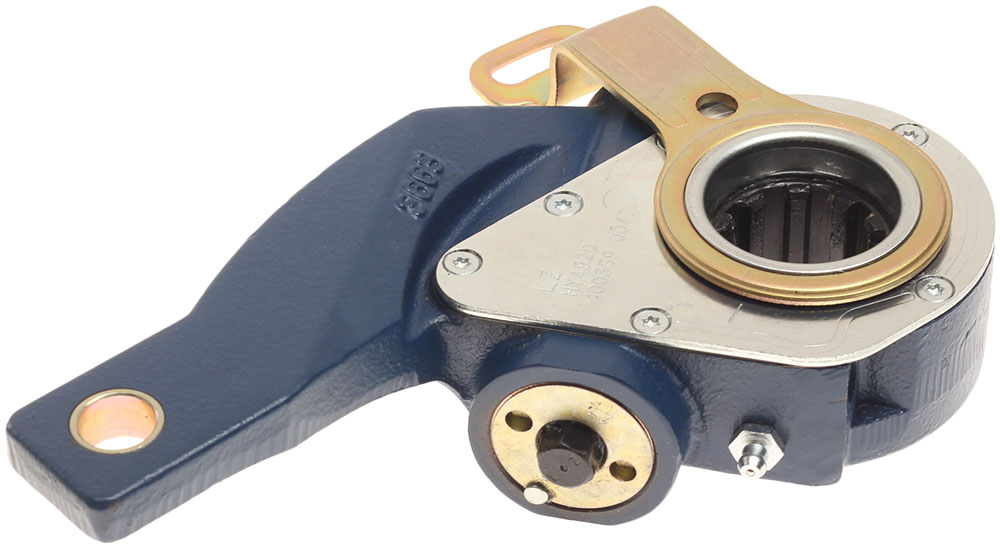
Adjustment lever with automatic adjustment
Thus, the lever automatically adjusts the position of the brake pads relative to the drum as the friction linings wear out, and up to the replacement of the linings does not require intervention.
Both types of levers are part of the front and rear wheel brakes, depending on the design, they can have from one to eight or more holes on the lever for rough adjustment of the brakes by rearranging the fork of the brake chamber rod or for installing chambers of various types. Since the lever is exposed to negative environmental influences during operation, it provides O-rings to protect internal parts from water, dirt, gases, etc.
Issues of selection, replacement and maintenance of the adjusting brake lever
The brake adjustment lever wears out and becomes unusable over time, which requires its replacement. Of course, the part can be repaired, but today in most cases it is easier and cheaper to buy and install a new lever than to restore the old one. For replacement, you should choose levers only of those types that were installed on the car earlier, however, if necessary, you can use analogues with suitable installation dimensions and characteristics. Replacing a manually adjustable lever with an automatic lever and vice versa in most cases is either impossible or requires modification of the brake wheel mechanism. If you plan to install a lever of another model or from another manufacturer, then you should change both levers on the axle at once, otherwise the adjustment of the gap on the right and left wheels can be made unevenly and with violations of the brakes.
The installation of the lever must be carried out in accordance with the instructions for the repair and maintenance of this particular vehicle. As a rule, this work is carried out in several steps: the lever is mounted on the axis of the expanding knuckle (which must be divorced under the action of springs), then the axis of the worm is rotated counterclockwise with the key until the hole on the lever is aligned with the fork of the TC rod, after which the lever is fastened with a fork and the axis of the worm is fixed with a retaining plate.
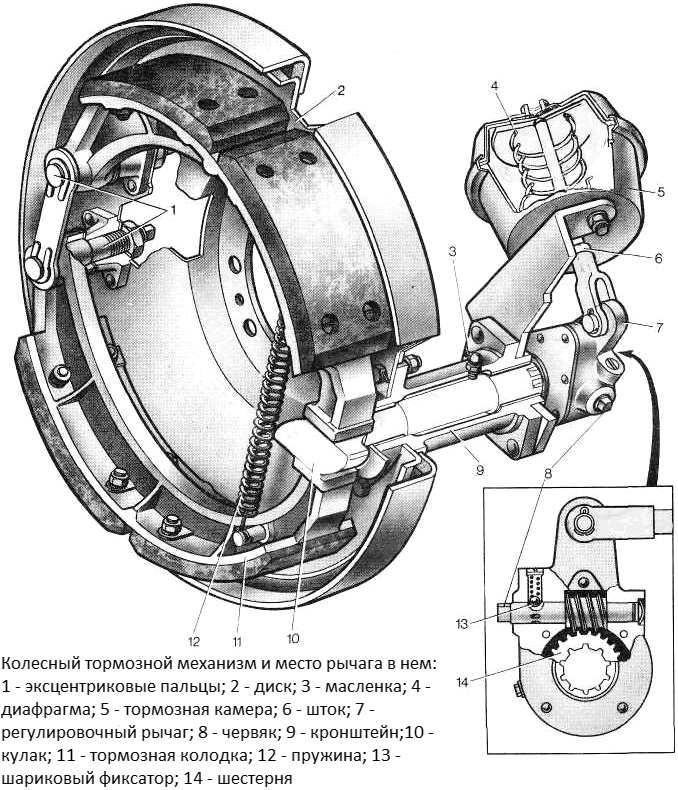
The wheel brake mechanism and the place of the adjusting lever in it
Devices of this type are similar in design to the signals discussed above, but have an additional detail - a straight horn ("horn"), spiral ("cochlea") or another type. The back of the horn is located on the side of the membrane, so the vibration of the membrane causes all the air located in the horn to vibrate - this provides sound emission of a certain spectral composition, the tone of the sound depends on the length and internal volume of the horn.
The most common are compact "snail" signals, which take up little space and have high power. Slightly less common are the "horn" signals, which, when enlarged, have an attractive appearance and can be used to decorate a car. Regardless of the type of horn, these ZSPs have all the advantages of conventional vibration signals, which ensured their popularity.
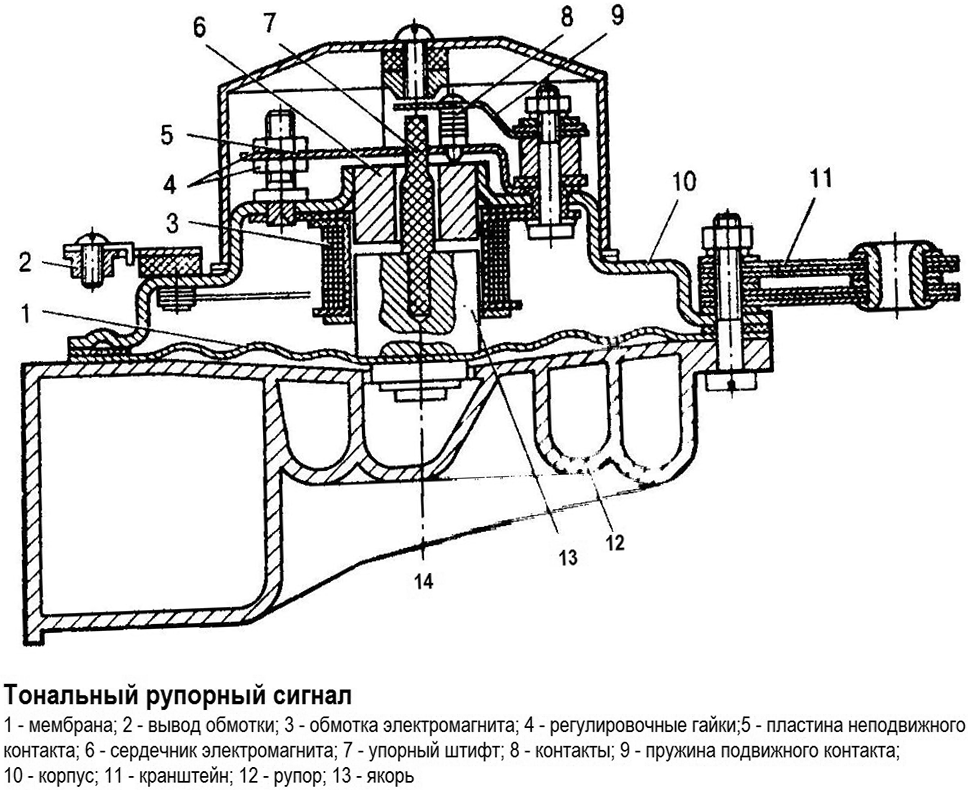
The design of the horn membrane sound signal
In the future, the lever with a manual regulator must be serviced - by turning the worm, adjust the distance between the pads and the drum. A lever with an automatic regulator requires manual intervention in two cases: when replacing friction linings and in case of jamming of the brakes during a long descent (due to friction, the drum heats up and expands, which leads to an increase in clearance - the lever automatically reduces the gap, but after stopping, the drum cools and shrinks, which can lead to jamming of the brakes). It is also periodically necessary to add lubricant to the levers through grease fittings (before squeezing the lubricant through the safety valve), usually lubrication is performed during seasonal maintenance using grease lubricants of certain brands.
With the right choice, proper installation and timely maintenance of the lever, wheel brakes will work reliably and efficiently in all operating conditions.
Post time: Jul-26-2023