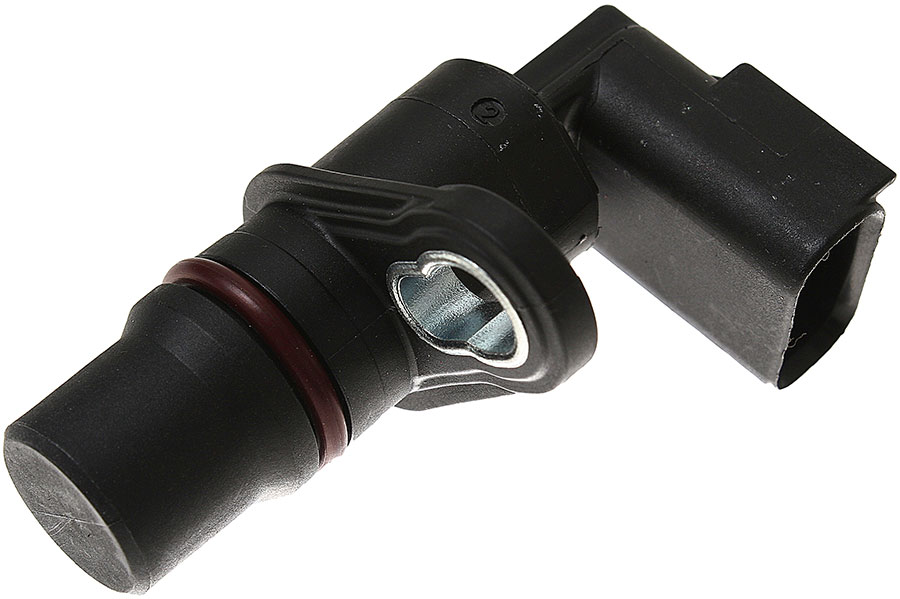
In any modern power unit, there is always a crankshaft position sensor, on the basis of which ignition and fuel injection systems are built. Read all about crankshaft position sensors, their types, design and operation, as well as the correct choice and replacement of these devices in the article.
Purpose and place of the crankshaft position sensor in the engine
Crankshaft position sensor (DPKV, synchronization sensor, reference start sensor) - a component of the electronic control system of the internal combustion engine; A sensor that monitors the performance characteristics of the crankshaft (position, speed), and ensures the functioning of the main systems of the power unit (ignition, power, gas distribution, etc.).
Modern internal combustion engines of all types for the most part are equipped with electronic control systems, which fully take over the operation of the unit in all modes. The most important place in such systems is occupied by sensors - special devices that track certain characteristics of the motor, and transmit data to the electronic control unit (ECU). Some sensors are critical to the operation of the power unit, including the crankshaft position sensor.
DPKV measures one parameter - the position of the crankshaft at each point in time. Based on the data obtained, the speed of the shaft and its angular velocity are determined. Receiving this information, the ECU solves a wide range of tasks:
● Determination of the TDC (or TDC) moment of the pistons of the first and/or fourth cylinders;
● Control of the fuel injection system - determination of the injection moment and the duration of the injectors;
● Ignition system control - determination of the ignition moment in each cylinder;
● Control of the variable valve timing system;
● Control of the operation of the components of the fuel vapor recovery system;
● Control and correction of the operation of other engine-related systems.
Thus, DPKV ensures the normal functioning of the power unit, fully determining the operation of its two main systems - ignition (only in gasoline engines) and fuel injection (in injectors and diesel engines). Also, the sensor turned out to be convenient for controlling other motor systems, the operation of which is directly or indirectly synchronized with the position and speed of the shaft. A faulty sensor can completely disrupt the operation of the engine, so it must be replaced. But before buying a new DPKV, you need to understand the types of these devices, their design and operation.
Types, design and principle of operation of DPKV
Regardless of the type and design, crankshaft position sensors consist of two parts:
● Position sensor;
● The master disk (sync disk, sync disk).
DPKV is placed in a plastic or aluminum case, which is mounted by means of a bracket next to the master disk. The sensor has a standard electrical connector for connecting to the vehicle's electrical system, the connector can be located both on the sensor body and on its own cable of short length. The sensor is fixed on the engine block or on a special bracket, it is located opposite the master disc and in the process of operation counts its teeth.
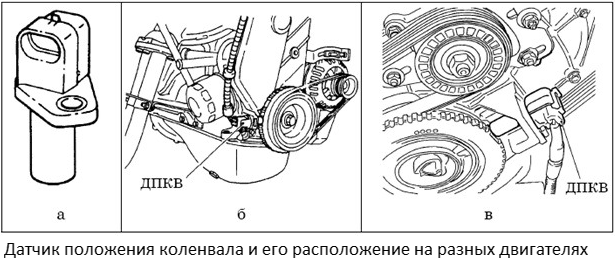
Crankshaft position sensor on different engines
The master disc is a pulley or wheel, along the periphery of which there are teeth of a square profile. The disc is rigidly fixed on the crankshaft pulley or directly on its toe, which ensures the rotation of both parts with the same frequency.
The operation of the sensor can be based on various physical phenomena and effects, the most widespread are devices of three types:
● Inductive (or magnetic);
● Based on the Hall effect;
● Optical (light).
Each of the types of sensors has its own design features and principle of operation.
Inductive (magnetic) DPKV. At the heart of the device is a magnetic core placed in a winding (coil). The operation of the sensor is based on the effect of electromagnetic induction. At rest, the magnetic field in the sensor is constant and there is no current in its winding. When the metal tooth of the master disk passes near the magnetic core, the magnetic field around the core changes abruptly, which leads to the induction of current in the winding. When the disc rotates, an alternating current of a particular frequency occurs at the output of the sensor, which is used by the ECU to determine the crankshaft speed and its position.
This is the simplest sensor design, it is widely used on all types of engines. The advantage of devices of this type is their operation without power supply - this makes it possible to connect them with just one pair of wires directly to the control unit.
Hall effect sensor. The sensor is based on an effect discovered by the American physicist Edwin Hall almost a century and a half ago: when current is passed through two opposite sides of a thin metal plate placed in a constant magnetic field, voltage appears on its other two sides. Modern sensors of this type are built on specialized Hall chips placed in a case with magnetic cores, and the master disks for them have magnetized teeth. The sensor works simply: at rest, there is zero voltage at the output of the sensor, when the magnetized tooth passes, voltage appears at the output. As in the previous case, when the master disk rotates, an alternating current arises at the output of the DPKV, which is supplied to the ECU.
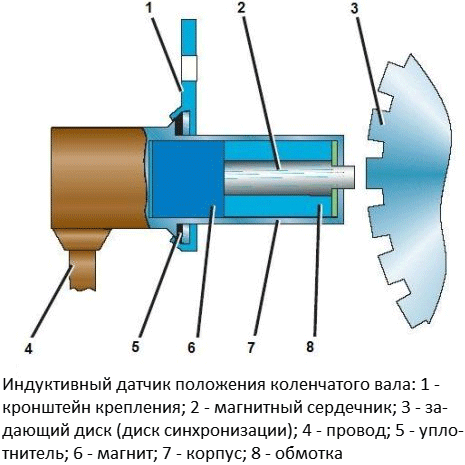
Inductive crankshaft position sensor
This is a more complex sensor, which, however, provides high measurement accuracy over the entire crankshaft speed range. Also, the Hall sensor requires a separate power supply for operation, so it is connected with three or four wires.
Optical sensors. The basis of the sensor is a pair of light source and receiver (LED and photodiode), in the gap between which there are teeth or holes of the master disk. The sensor works simply: the disk, when rotating at varying intervals, outshines the LED, as a result of which a pulsed current is formed at the output of the photodiode - it is used by the electronic unit for measurement.
Currently, optical sensors are of limited use, due to the difficult conditions of their operation in the engine - high dustiness, the possibility of smoke, contamination with liquids, road dirt, etc.
Standardized master disks are used to work with sensors. Such a disc is divided into 60 teeth located every 6 degrees, while in one place of the disc there are no two teeth (sync disc type 60-2) - this pass is the beginning of the crankshaft rotation and ensures synchronization of the sensor, ECU and associated systems. Usually, the first tooth after skipping coincides with the position of the piston of the first or last cylinder at TDC or TDC. There are also discs with two skips of teeth located at an angle of 180 degrees to each other (sync disc type 60-2-2), such discs are used on some types of diesel power units.
The master discs for inductive sensors are made of steel, sometimes at the same time as the crankshaft pulley. Discs for Hall sensors are often made of plastic, and permanent magnets are located in their teeth.
In conclusion, we note that DPKV is often used both on the crankshaft and on the camshaft, in the latter case, it is used to monitor the position and speed of the camshaft and make adjustments to the operation of the gas distribution mechanism.
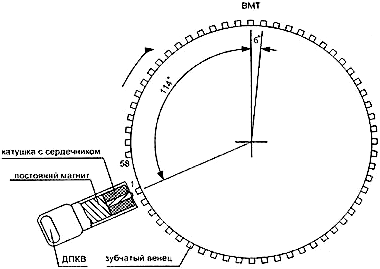
Installation of inductive type DPKV and master disk
How to choose and replace the crankshaft sensor correctly
DPKV plays a key role in the motor, sensor malfunctions lead to a sharp deterioration in engine operation (difficult start, unstable operation, decrease in power characteristics, detonation, etc.). And in some cases, if the DPKV fails, the engine becomes completely inoperable (as indicated by the Check Engine signal). If there are described problems with the operation of the engine, then you should check the crankshaft sensor, and in case of its malfunction, perform a replacement.
First, you need to inspect the sensor, check the integrity of its body, connector and wires. The inductive sensor can be checked with a tester - it is enough to measure the resistance of the winding, which the working sensor has in the range of 0.6-1.0 kOhm. The Hall sensor cannot be checked in this way, its diagnostics can only be performed on special equipment. But the easiest way is to install a new sensor, and if the engine starts, then the problem was precisely in the malfunction of the old DPKV.
To replace, you should choose a sensor only of the type that was installed on the car and recommended by the automaker. Sensors of another model may not fit into place or make significant errors in measurements, and, as a result, disrupt the operation of the motor. The DPKV should be changed in accordance with the vehicle repair instructions. Usually, it is enough to disconnect the electrical connector, unscrew one or two screws / bolts, remove the sensor and install a new one instead. The new sensor should be located at a distance of 0.5-1.5 mm from the end of the master disc (the exact distance is indicated in the instructions), this distance can be adjusted with washers or in another way. With the right choice of DPKV and its replacement, the engine will immediately start working, only in some cases it will be necessary to calibrate the sensor and reset the error codes.
Post time: Jul-13-2023