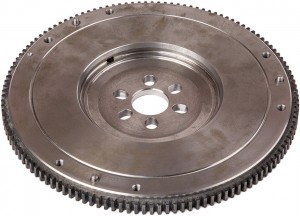
In any piston internal combustion engine, you can find a massive part of the crank mechanism and other related systems - the flywheel. Read all about flywheels, their existing types, design and principle of operation, as well as the selection, repair and replacement of these parts in this article.
The role and place of the flywheel in the engine
Flywheel (flywheel) - assembly of the crank mechanism (KShM), clutch and piston internal combustion engine launch system; Located on the shank of the crankshaft is a metal disc of large mass with a ring gear, which ensures the stable operation of the motor due to the accumulation and subsequent return of kinetic energy.
The operation of piston internal combustion engines is uneven - in each of its cylinders, four strokes are made in two revolutions of the shaft, and in each stroke the speed of the piston is different. To eliminate the uneven rotation of the crankshaft, the same strokes in different cylinders are spaced apart in time, and an additional unit is introduced into the KShM - a flywheel made in the form of a massive metal wheel fixed on the rear of the crankshaft.
The flywheel solves several key tasks:
● Ensuring the uniformity of the angular velocity of the crankshaft;
● Ensuring the removal of pistons from dead points;
● Transmission of torque from the crankshaft to the clutch mechanism and then to the gearbox;
● Transmission of torque from the starter gear to the crankshaft when starting the power unit;
● Some types of parts are the damping of torsional vibrations and vibrations, the decoupling of the KShM and the transmission of the vehicle.
This part, due to its considerable mass, accumulates the kinetic energy obtained during the working stroke and gives it to the crankshaft on the remaining three strokes - this ensures both the alignment and stability of the angular velocity of the crankshaft, and the withdrawal of pistons from TDC and TDC (due to the emerging inertial forces). Also, it is through the flywheel that the engine communicates with the transmission of the car and the transmission of torque from the gear of the electric starter to the crankshaft when the engine is started. The flywheel is critical for the normal operation of the vehicle, so if it malfunctions, it is necessary to carry out repairs or complete replacements as soon as possible. But before starting repair work, you should understand the existing types, designs and features of the flywheels of modern internal combustion engines.
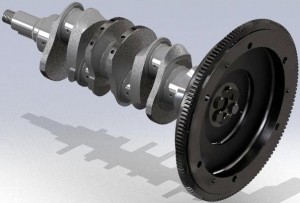
Flywheel assembly with engine crankshaft
Types and structure of flywheels
On modern motors, flywheels of various designs are used, but three types of these parts are most widespread:
● Solid;
● Lightweight;
● Damper (or dual-mass).
The simplest device has solid flywheels, which are used on most piston internal combustion engines - from small cars to the most powerful industrial, diesel and marine engines. The basis of the design is a cast iron or steel disc with a diameter of 30-40 cm or more, in the center of which there is a seat for installation on the crankshaft shank, and a crown is pressed on the periphery. The seat for the crankshaft is usually made in the form of an extension (hub), in the center of which there is a hole of large diameter, and around the circumference there are 4-12 or more holes for bolts, through which the flywheel is fixed on the flange of the shaft shank. On the outer surface of the flywheel, there is a place for installing the clutch and an annular contact pad for the clutch driven disc is formed. On the periphery of the flywheel, a steel ring gear is pressed in, through which, at the time of starting, torque is transmitted from the starter gear to the crankshaft.
Usually, in manufacturing, the flywheel is balanced to prevent runouts during engine operation. When balancing in different places of the flywheel, excess metal is removed (drilling), and for the purpose of balancing in a certain position, the clutch and other parts (if provided) are installed. In the future, the orientation of the flywheel and clutch should not change, otherwise there will be an imbalance that is dangerous for the crankshaft and the entire engine.
Lightweight flywheels have a similar design, but windows of various shapes and sizes are made in them to reduce weight. Sampling the metal of the flywheel in order to reduce its weight is usually performed for the purpose of tuning and boosting the engine. The installation of such a flywheel somewhat reduces the stability of the power unit in transient modes, but provides a quick set of maximum speeds and, in general, has a positive effect on power characteristics. However, the installation of a lightweight flywheel can only be carried out in parallel with the performance of other work on tuning / boosting the engine.
Dual-mass flywheels have a much more complex design - they include torsional vibration dampers and dampers that are different in design and principle of operation. In the simplest case, this unit consists of two disks (slave and master), between which there is a torsional vibration damper - one or more arc (rolled into a ring or curved by an arc) twisted springs. In more complex designs, there are a number of gears between the discs, which act as a planetary transmission, and the number of springs can reach a dozen or more. The dual-mass flywheel, like the conventional one, is mounted on the crankshaft shank and holds the clutch.
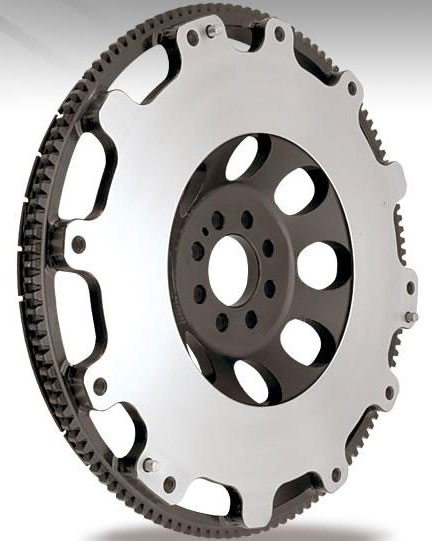
Lightweight flywheelft
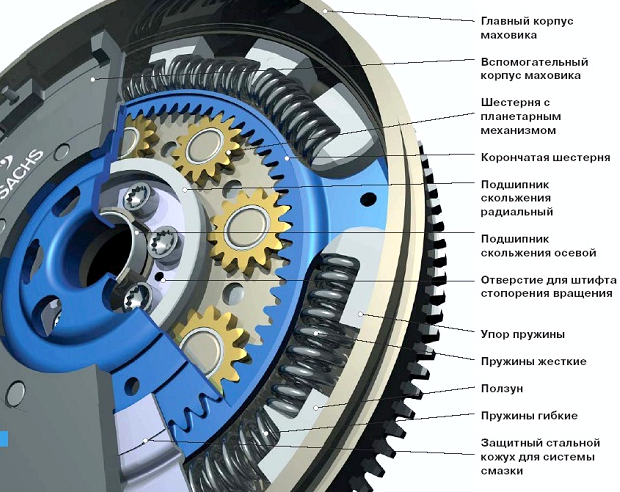
Dual-mass flywheel design
The damper flywheel works quite simply. The drive disc is connected directly to the crankshaft flange, receiving torque from it, as well as all vibrations, vibrations and shocks that occur in transient conditions. The torque from the drive disc to the slave is transmitted through springs, but due to their elasticity, they absorb a significant part of vibrations, shocks and vibrations, that is, they perform the functions of a damper. As a result of this decoupling, the driven disc, as well as the clutch and transmission connected to it, rotate more evenly, without vibrations and vibrations.
Currently, dual-mass flywheels, despite their complex design and relatively high cost, are increasingly installed on the engines of cars and trucks. The growing popularity of these parts is due to their better quality of work and protection of the transmission from negative influences from the power unit. However, flywheels of solid construction, due to their price, reliability and simplicity, are very widely used on budget cars, most tractors, trucks and other equipment.
Flywheel selection, replacement and maintenance issues
During the operation of the engine, the flywheel is subjected to significant mechanical loads, so over time, all sorts of malfunctions occur in it - cracks, wear of the contact surface with the clutch driven disc, wear and breakage of the crown teeth, deformations and even complete destruction (cast iron parts are subject to this). Malfunctions of the flywheel are manifested by an increase in the level of vibrations and noise during engine operation, deterioration of the clutch, deterioration or inability to start the engine with a starter (due to wear of the ring gear), etc.
Most often in flywheels of a solid structure, the cause of the problem is the ring gear, as well as cracks and breakdowns of the disc itself. In the normal state of the flywheel, the crown can be replaced, a part of the same type and model that stood earlier should be taken for replacement. If necessary, you can use a crown with a different number of teeth, but such a replacement is not always possible. Dismantling strictly the crown is usually performed mechanically - by hammer blows through a chisel or other tool. The installation of a new crown is carried out with its heating - due to thermal expansion, the part will easily fall into place, and after cooling it will be securely fixed on the flywheel.
In damper flywheels, more complex malfunctions often occur - breakage or complete destruction of arc springs, wear of bearings, wear of rubbing parts of discs, etc. In most cases, the dual-mass flywheel cannot be repaired, but is replaced in the assembly. In some situations, it is possible to replace the crown and bearings, but it is better to entrust these works to specialists. Diagnostics of the damper flywheel is carried out both on the engine and on the removed part. First of all, the angle of deflection of the driven flywheel and backlash is checked, if the angle is too large or, on the contrary, the flywheel is jammed, then the part must be replaced.
All diagnostic work and replacement of the flywheel must be carried out in accordance with the instructions for repair and maintenance of the vehicle. To access the part, in most cases, it is necessary to dismantle the gearbox and clutch, which is associated with additional time and effort. When installing a new flywheel, it is necessary to observe the orientation of the clutch, as well as use certain types of fasteners and, if necessary, types of lubricants. If the flywheel is selected and replaced correctly, then the engine and transmission will work reliably, confidently performing their functions.
Post time: Jul-13-2023