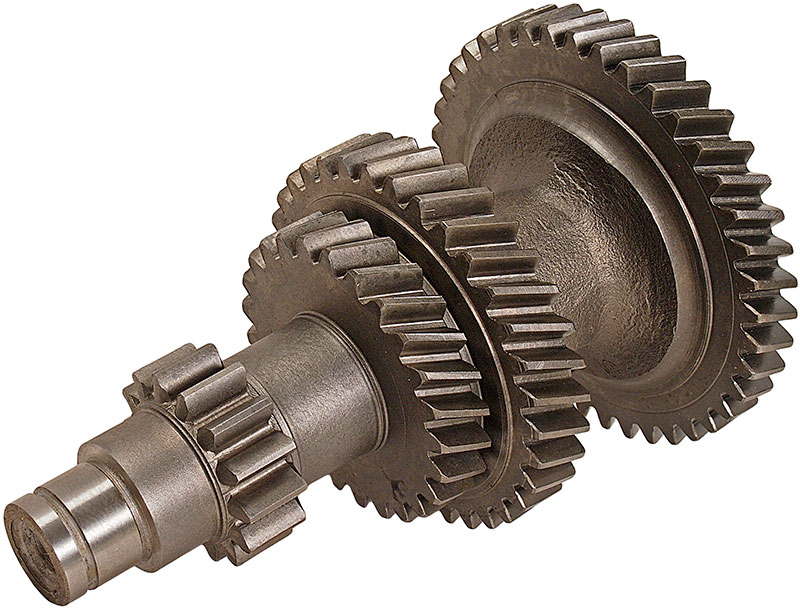
The transmission and change of torque in the gearbox is carried out by gears of various diameters. The gears of the gearbox are assembled in the so-called blocks - read about the gear blocks of the boxes, their structure and functioning, as well as their maintenance and repair, in the article.
The purpose of the gear blocks and their place in the gearbox
Despite the increasing prevalence of automatic transmissions, manual (or manual) transmissions do not lose their popularity and relevance. The reason for this is simple - manual transmissions are simple in design, reliable and provide ample opportunities for driving. And besides, mechanical boxes are easier to repair and maintain.
As you know, in manual transmissions, shafts with gears of various diameters are used to change the torque, which can engage with each other. When shifting gears, one or another pair of gears is engaged, and depending on the ratio of their diameters (and the number of teeth), the torque coming to the drive axles of the car changes. The number of pairs of gears in the manual gearbox of cars and trucks can range from four (in old 3-speed gearboxes) to seven (in modern mass 6-speed gearboxes), with one of the pairs being used to engage reverse gear. In the boxes of tractors and various machines of special machines, the number of pairs of gears can reach a dozen or more.
The gears in the box are located on the shafts (freely or rigidly, this is described below), and to increase reliability and simplify the design, some gears are assembled into a single structure - a block of gears.
The gearbox gear block is a one-piece structure of 2 or more gears that rotate at the same angular velocity during the operation of the box. Combining gears into blocks is done for several reasons:
- Simplification of the design of the box with a reduction in the number of components used. Since one gear needs to provide its own fasteners and drive, combining into a block makes separate parts for each gear unnecessary;
- Improving the manufacturability of the production of gearbox parts;
- Improving the reliability of the transmission (again by reducing components and simplifying the design).
However, gear blocks have one drawback: if one of the gears breaks down, you have to change the entire block. Of course, this increases the cost of repairs, but such a solution pays off many times over for the reasons described above.
Let us consider in more detail the existing types and design features of manual transmission gear blocks.
Types and design features of gear blocks
Gear blocks can be divided into groups according to applicability and purpose:
- Intermediate shaft gear blocks;
- Driven (secondary) shaft gear blocks;
- Reverse gear blocks.
In this case, the drive (primary) shaft is usually made at the same time with the gear, so that a separate gear block does not stand out in it.
KP intermediate shafts can be divided into two types according to the design of gear blocks:
- Solid - gears and shaft form a single whole;
- Typesetting - gear blocks and shaft are independent parts, assembled into one structure.
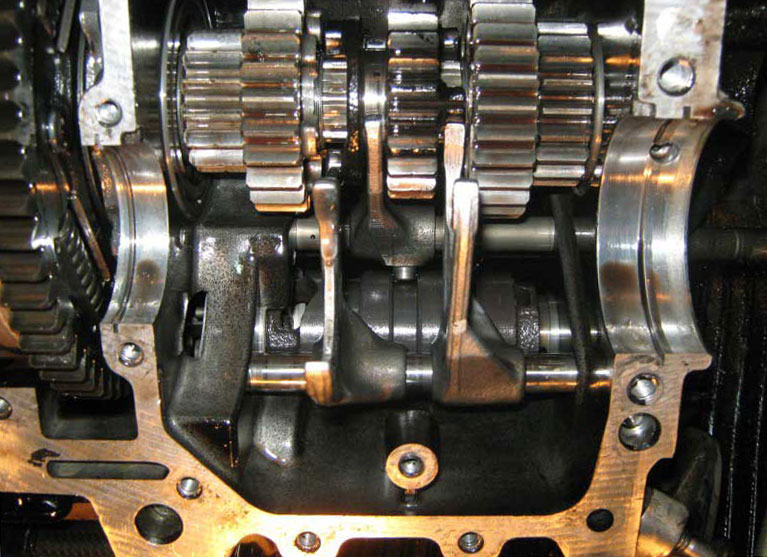
In the first case, the shaft and gears are made of the same workpiece, so they are a single non-separable part. Such shafts are the most common, as they have the simplest design and low price. In the second case, the structure is assembled from a shaft and two or three or more gear blocks fixed on it. But in any case, the gear blocks on the countershaft rotate as a whole.
Driven (secondary) shafts are only typesetting, and the gear blocks can rotate freely on the shaft - they are fixed with the help of couplings only at the moment of switching on a particular gear. Due to the design features of the manual transmission, the driven shaft blocks do not contain more than 2 gears, and usually these are gears of close gears. For example, the gears of the 1st and 2nd, 3rd and 4th gears, as well as the 2nd and 3rd gears (if the gear of the 1st gear is located separately), etc., can be combined into blocks. At the same time, in automobile 5-speed manual transmissions, the gear of the 5th stage is performed separately, since the 4th gear is usually straight and when it is turned on, the intermediate shaft is "turned off" from the gearbox (in this case, the torque flow comes directly from the drive shaft on the slave).
Reverse gear units always contain only two gears, one of which engages with a specific countershaft gear and the second with a secondary shaft gear. As a result of this connection, the torque flow is inverted and the vehicle can be reversed.
All gearbox gear blocks have a fundamentally identical design - they are machined from a single steel billet, and only in some cases have additional elements for fastening to the shaft or engaging with couplings, as well as for installing bearings. The gearbox uses both helical gears and conventional spur gears. In modern boxes, helical gears are more often used, which create a lower noise level during operation. However, reverse gears are most often performed spur, as they operate at low speeds and the noise level is not critical for them. In an old-style manual transmission, all or almost all gears are spur.
Gear blocks are made of certain grades of steel, as they experience enormous loads during operation. Also, structurally, gear blocks are large and massive parts that successfully withstand shock and other mechanical, as well as thermal loads. But despite this, gear blocks require periodic repair or replacement.
Issues of repair and replacement of gear blocks
Gear blocks operate in hard conditions, so various malfunctions can occur in them over time. First of all, gears are characterized by tooth wear, which, in principle, cannot be prevented. With gentle operation of the vehicle, the wear of the gear blocks is not too intensive, so they can work for decades, and the replacement of these parts due to wear is rarely required.
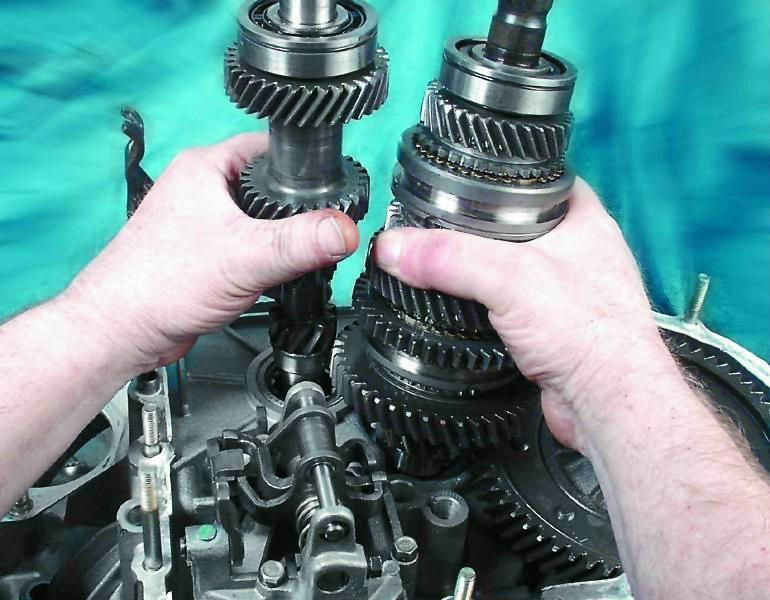
More often, the reason for replacing gears is their deformation, cracking, breakage and chipping of teeth, or complete destruction (which usually occurs when operating a gearbox with crumbled teeth). All these malfunctions are manifested by increased gearbox noise, the appearance of extraneous sounds, grinding or crunching during operation and gearing, as well as poor operation of the gearbox in one or more gears. In all these cases, the gearbox should be repaired and the gear block should be replaced. We will not consider the procedure for performing repairs here, since it depends on the type and model of the box, a full description can be found in the instructions for maintenance and repair of the vehicle.
To extend the service life of the gear blocks and the entire box, routine maintenance of the transmission should be performed, as well as carefully and competently operate the vehicle - correctly turn on and off gears, drive at the optimal speed for current conditions, etc.
Post time: Aug-27-2023