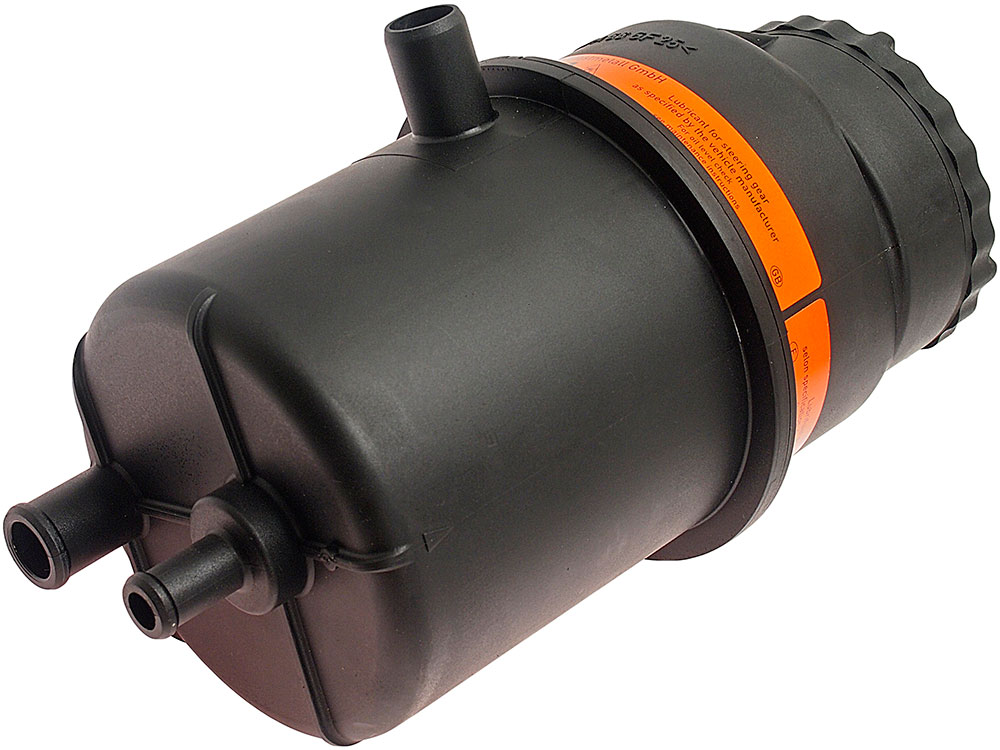
Almost all domestic trucks and buses use power steering, which must be equipped with tanks of various designs. Read about power steering pump tanks, their existing types, functionality and design features, maintenance and repair in the article.
Purpose and functionality of the power steering pump tank
Since the 1960s, most domestic trucks and buses have been equipped with power steering (GUR) - this system greatly facilitated the operation of heavy machines, reduced fatigue and increased the efficiency of work. Already at that time, there were two options for the layout of the power steering system - with a separate tank and with a tank located on the power steering pump housing. Today, both options are widely used, which will be discussed below.
Regardless of the type and design, all power steering pump tanks have five key functions:
- Storage is sufficient for the operation of the power steering of the liquid reserve;
- Cleaning the working fluid from wear products of power steering parts - this task is solved by the built-in filter element;
- Compensation for the thermal expansion of the fluid during the active operation of the power steering;
- Compensation for minor leaks of power steering fluid;
- Release of increased pressure in the system when the filter is clogged, the system is aired or if the maximum oil level rises.
In general, the reservoir ensures the normal operation of the pump and the entire power steering. This part is responsible not only for storing the necessary supply of oil, but also ensures its uninterrupted supply to the pump, cleaning, operation of the power steering even with excessive clogging of the filter, etc.
Types and structure of tanks
As already mentioned, at present, two main types of power steering pump tanks are actively used:
- Tanks mounted directly on the pump body;
- Separate tanks connected to the pump by hoses.
Tanks of the first type are equipped with KAMAZ vehicles (with KAMAZ engines), ZIL (130, 131, model range "Bychok" and others), "Ural", KrAZ and others, as well as buses LAZ, LiAZ, PAZ, NefAZ and others. In all these cars and buses, two types of tanks are used:
- Oval — used mainly on KAMAZ trucks, Urals, KrAZ trucks and buses;
- Cylindrical - used mainly on ZIL cars.
Structurally, both types of tanks are fundamentally the same. The basis of the tank is a steel stamped body with a set of holes. From above, the tank is closed with a lid (through a gasket), which is fixed with a stud passed through the tank and a lamb nut (ZIL) or a long bolt (KAMAZ). The stud or bolt is screwed into the thread on the pump manifold, which is located at the bottom of the tank (through the gasket). The manifold itself is held by four bolts screwed into the threads on the pump body, these bolts fix the entire tank on the pump. For sealing, there is a sealing gasket between the tank and the pump housing.
Inside the tank there is a filter, which is mounted directly on the pump manifold (in KAMAZ trucks) or on the inlet fitting (in ZIL). There are two types of filters:
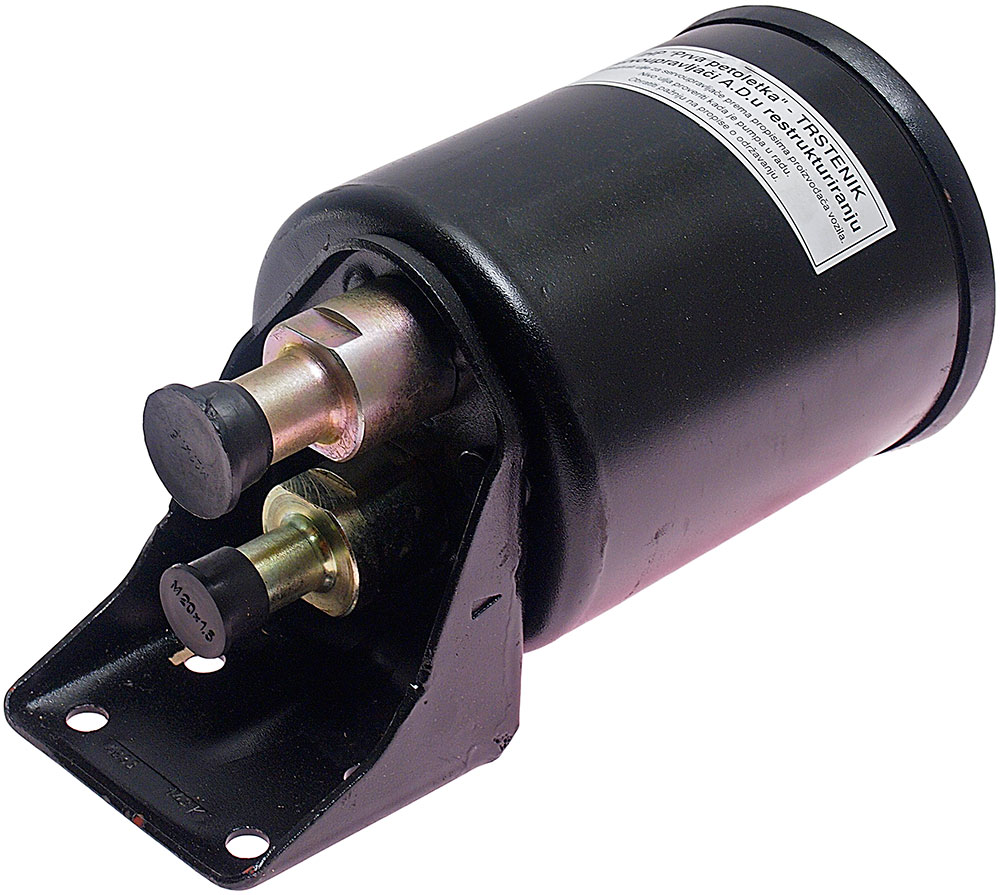
- Mesh - are a series of round mesh filter elements assembled in a package, structurally the filter is combined with a safety valve and its spring. These filters are used on early modifications of cars;
- Paper - ordinary cylindrical filters with a paper filter element, used on current car modifications.
The pump cover has a filler neck with a plug, a hole for a stud or bolt, as well as a hole for mounting a safety valve. A mesh filler filter is installed under the neck, which provides primary cleaning of the power steering liquid poured into the tank.
In the wall of the tank, closer to its bottom, there is an inlet fitting, inside the tank it can be connected to the filter or to the pump manifold. Through this fitting, the working fluid flows from the power hydraulic cylinder or rack into the tank filter, where it is cleaned and fed to the discharge section of the pump.
Separate tanks are used on KAMAZ vehicles with Cummins, MAZ engines, as well as on the previously mentioned buses of most current modifications. These tanks are divided into two types:
- Steel stamped tanks of early and many current models of cars and buses;
- Modern plastic tanks of current modifications of cars and buses.
Metal tanks are usually cylindrical in shape, they are based on a stamped body with intake and exhaust fittings (the exhaust is usually located on the side, the intake - in the bottom), which is closed with a lid. The lid is fixed by the stud and nuts passing through the entire tank, to seal the tank, the lid is installed through a gasket. Inside the tank there is a filter with a paper filter element, the filter is pressed against the inlet fitting by a spring (this whole structure forms a safety valve that ensures the flow of oil into the tank when the filter is clogged). On the lid there is a filler neck with a filler filter. On some models of tanks, the neck is made on the wall.
Plastic tanks can be cylindrical or rectangular, usually they are non-separable. In the lower part of the tank, fittings are cast to connect the hoses of the power steering system, in some models of tanks, one fitting can be located on the side wall. In the upper wall there is a filler neck and a filter cover (to replace it in case of clogging).
Installation of tanks of both types is carried out on special brackets with the help of clamps. Some metal tanks carry a bracket that is bolted in the engine compartment or in another convenient place.
Tanks of all types function in the same way. When the engine starts, the oil from the tank enters the pump, passes through the system and returns to the tank from the filter side, here it is cleaned (due to the pressure that the pump tells the oil) and again enters the pump. When the filter is clogged, the oil pressure in this unit rises and at some point overcomes the compression force of the spring - the filter rises and the oil flows freely into the tank. In this case, the oil is not cleaned, which is fraught with accelerated wear of the power steering parts, so the filter must be replaced as soon as possible. If the pressure rises in the power steering pump reservoir or too much liquid is flooded, a safety valve is triggered through which excess oil is ejected.
In general, power steering pump tanks are extremely simple and reliable in operation, but they also need periodic maintenance or repair.
Issues of maintenance and repair of power steering pump tanks
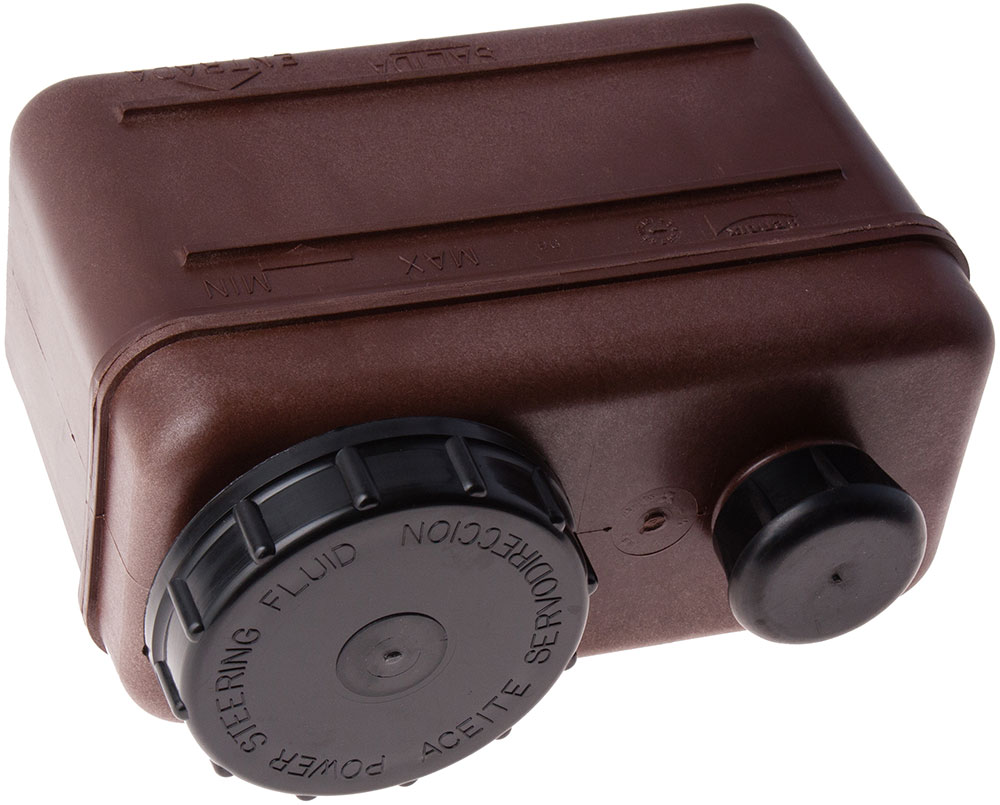
When operating a car, the tank should be checked for tightness and integrity, as well as for the tightness of the connection to the pump or to the pipelines. If cracks, leaks, corrosion, serious deformations and other damage are found, the tank assembly should be replaced. If leaky connections are found, the gaskets must be replaced or the hoses must be re-fastened to the fittings.
To replace the tank, it is necessary to drain the fluid from the power steering, and dismantle. The procedure for removing the tank depends on its type:
- For tanks mounted on the pump, you need to dismantle the cover (unscrew the bolt / lamb) and unscrew the four bolts holding the tank itself and the manifold on the pump;
- For individual tanks, remove the clamp or unscrew the bolts from the bracket.
Before installing the tank, check all gaskets, and if they are in poor condition, install new ones.
With a frequency of 60-100 thousand km (depending on the model of this particular car and the design of the tank), the filter must be changed or cleaned. Paper filters must be replaced, strainers must be dismantled, disassembled, washed and cleaned.
It is important to properly replenish the oil supply and check the oil level in the tank. Pour liquid into the tank only when the engine is running and idling, and the wheels are installed straight. For filling, it is necessary to unscrew the plug and fill the tank with oil strictly to the specified level (not lower and not higher).
Proper operation of the power steering, regular replacement of the filter and timely replacement of the tank are the basis for reliable operation of the power steering in any conditions.
Post time: Aug-27-2023