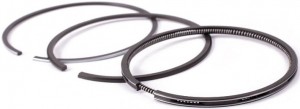
In any modern piston engine there are parts that ensure the tightness of the combustion chamber and lubrication of the cylinders - piston rings. Read all about piston rings, their existing types, design features and operation, as well as the correct selection and replacement of rings in the proposed article.
What are piston rings?
Piston rings - parts of the cylinder-piston group (CPG) of an internal combustion engine; metal detachable rings mounted on pistons in order to seal the combustion chamber, reduce engine oil losses and minimize the amount of exhaust gases entering the crankcase.
For the normal operation of a piston internal combustion engine, it is critically important that a pressure exceeding a certain minimum level is created in the combustion chamber at the end of the compression stroke (when the piston reaches top dead center) - this parameter is called compression. For gasoline engines, compression lies in the range of 9-12 atmospheres, for diesel units this parameter is 22-32 atmospheres. To achieve the necessary compression, it is necessary to ensure the sealing of the combustion chamber - this problem is solved by piston rings.
Piston rings perform several key functions:
● Sealing of the combustion chamber - the size of the ring is selected exactly according to the inner diameter of the cylinder, which prevents the breakthrough of gases from the combustion chamber into the crankcase;
● Reduction of friction forces - the friction area of the rings on the walls of the cylinder is much smaller than the piston area, which reduces the friction losses of the CPG parts;
● Compensation for the thermal expansion of CPG materials - pistons and cylinders are made of various alloys with different coefficients of thermal expansion, the introduction of rings prevents jamming of the pistons and changes in compression when the engine temperature rises and falls;
● Lubrication of the cylinder walls and removal of excess oil (which prevents it from entering the combustion chambers and reduces oil loss due to waste) - rings of a special design ensure the removal of excess oil from the cylinder walls formed during engine operation, but leave the oil film necessary to reduce friction;
● Cooling of the piston walls - part of the heat from the piston is removed to the cylinder walls through the rings.
It is easy to see that the piston rings play a crucial role in the operation of the CPG and the functioning of the entire power unit. Any malfunctions and wear of the rings are manifested by a loss of engine power and a general deterioration in its operation, so these parts must be replaced. But before buying or ordering new rings, you should understand the existing types of these parts, their design and features of work.
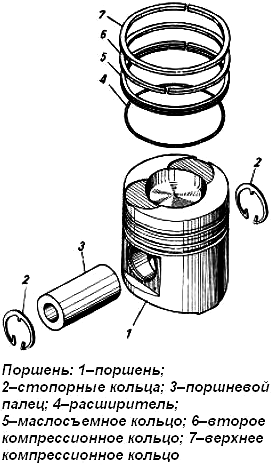
Piston and piston rings
Types, design and principle of operation of piston rings
Two types of rings are installed on one piston:
● Compression (upper);
● Oil scrapers (lower).
All rings are located in transverse grooves (grooves) of a rectangular profile, made closer to the piston head. Rings of different types differ in design and purpose.
Compression rings provide sealing of the combustion chamber, one, two or three rings can be installed on one piston (one on two-stroke internal combustion engines of motorcycles, two on most modern four-stroke engines, three on some diesel engines), they are located in the upper part of the piston. Structurally, compression rings are very simple: this is a metal detachable ring, the cut of which is made in the form of a simple (straight, oblique) or complex lock, on some rings in the lock there is a recess for a stopper. The lock has a small gap (several micrometers), which serves to compensate for the thermal expansion of the part during engine operation.
Rings are made of steel or special grades of cast iron, their outer (working) surface can have a different profile:
● Simple flat - in this case, the ring has a rectangular cross-section or a section in the form of an irregular quadrilateral;
● Radius (barrel-shaped) - the outer surface of the ring is an arc of a circle of large radius;
● With a chamfer - a chamfer of small height is made on the outer surface;
● "Minute" rings - the outer surface has a slope to the top, the angle of inclination is several tens of minutes of arc, due to which the rings got their name.
The flat profile has upper compression rings, which are forced to work at high temperatures and pressures in conditions of insufficient lubrication. To reduce wear, the working surface of the part is chrome-plated, phosphated, tin coated or otherwise treated. Such a ring is completely adjacent to the cylinder mirror during operation, providing sealing and heat removal from the piston.
The lower rings often have a more complex profile. Barrel rings have less friction resistance while maintaining a sufficient degree of sealing. "Minute" rings, due to the inclination of the working surface, reduce frictional forces: when the piston moves down (on the working stroke), the ring slides along the cylinder mirror with its pointed edge, and when moving upwards, the ring is squeezed out of the cylinder mirror due to the resulting oil wedge.
Oil scraper rings ensure the correct distribution of the oil film over the surface of the cylinder and prevent oil from entering the combustion chamber (remove it from the cylinder mirror). Only one ring is used on one piston, these parts are not on the pistons of two-stroke engines (since oil is added directly to gasoline). Usually, oil scraper rings have a composite design, which includes the rings themselves and expanders.
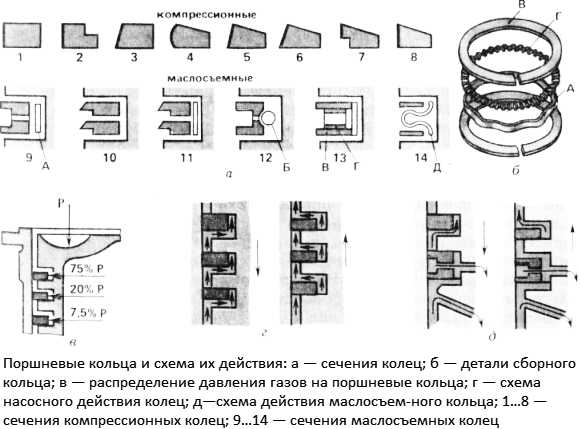
Piston rings and their scheme of action
Oil scraper rings are:
● One-piece - a U-shaped ring facing the base to the piston. At the base there is a series of round or elongated holes through which oil drains is carried out;
● Composite - two thin (split) rings are used, between which there is a spacer element.
Spacer elements are:
● Radial - provide pressure of the rings to the wall of the cylinder;
● Axial - used only in conjunction with composite rings, provide unclenching of rings;
● Tangential - combined spacer elements, provide simultaneous expansion of the rings and their pressure against the cylinder wall.
The spacer elements are plate (flat) or coiled springs embedded between or under the rings, only one or two springs of various types can be used in the oil scraper ring.
The oil scraper ring is pressed against the cylinder wall and, due to its design, ensures the removal of excess oil film. The collected oil enters the groove through the holes in the ring, from where it drains into the engine crankcase through holes in the piston wall. At the same time, part of the oil remains in the form of a thin oil film on the cylinder wall, which reduces friction throughout the CPG.
How to choose and replace piston rings
During engine operation, piston rings are subjected to significant mechanical and thermal loads, which leads to their gradual wear and loss of performance. As the rings wear out, they cease to perform their functions, which leads to a decrease in compression, seepage of gases into the crankcase and oil into the combustion chamber. Also a serious problem is the "coking" of the rings (jamming due to the accumulation of carbon deposits in the grooves of the piston). As a result, the engine loses power and throttle response, the exhaust acquires a characteristic gray or even black tint, and fuel and oil consumption increases. When these signs appear, it is necessary to diagnose the engine - check the compression, inspect the candles and some other parts. If the compression is too low, the candles are splashed with oil and there are problems with the operation of the power unit, then the piston rings must be replaced.
For replacement, you should choose rings only of those types and catalog numbers that are provided for this particular engine. It should be borne in mind that after performing a major overhaul of the engine with boring cylinders, it is necessary to use repair size rings suitable for new pistons.
Replacement of rings must be carried out in accordance with the instructions for the repair of the power unit. In general, this work requires disassembling the engine and recessing the pistons. Old rings are removed and grooves are thoroughly cleaned. New rings must be placed in accordance with the instructions of the "Top" or "Up" marks on them. When installing the rings, the gaps between the side surface of the part and the wall of the groove in the piston, as well as in the lock of the ring inserted into the cylinder, are checked. All clearances must lie within the limits established for the motor. The rings are located on the piston so that their locks do not lie on the same line and do not fall on the axis of the finger holes - this is how a labyrinth is formed that prevents the breakthrough of gases from the combustion chamber.
When mounting a piston with new rings in the cylinder, a special mandrel should be used that presses the rings against the piston. After replacing the piston rings, it is recommended to run in the engine - do not overestimate the speed for the first 800-1000 km and load the engine at half power, at the end of the break-in, you should change the engine oil.
With the right choice and replacement of piston rings, the engine will regain its former power and will work confidently in all modes.
Post time: Jul-13-2023