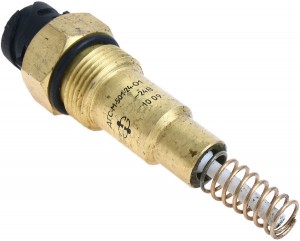
In modern cars, tractors and other equipment, various hydraulic systems are widely used. An important role in the operation of these systems is played by sensors-hydraulic alarms - read all about these devices, their existing types, design and operation, as well as the selection and replacement of sensors, in the article
What is a hydraulic alarm sensor?
Sensor-hydrosignaling device (sensor-relay, sensor-indicator of liquid level) - an element of electronic control, monitoring and indication systems of hydraulic systems of vehicles; A threshold sensor that sends a signal to an indicator or actuator(s) when the liquid reaches a predetermined threshold level.
In any vehicle there are several hydraulic systems and components: power hydraulic systems (in trucks, tractors and various equipment), lubrication and cooling systems of the power unit, power supply system, window washers, power steering and others. In some systems, the liquid level must be monitored constantly (as in a fuel tank), while in others it is only necessary to obtain information about the presence or absence of liquid, or about the liquid overcoming a certain level (exceeding or falling). The first task is solved by continuous level sensors, and for the second, hydraulic alarm sensors (DGS) or liquid level sensors are used.
DGS are installed in expansion tanks, engine crankcase and other elements of hydraulic systems. When the liquid reaches a certain level, the sensor is triggered, it closes or opens the circuit, providing an on/off indicator on the dashboard (for example, an oil drop indicator), or turning on/off actuators - pumps, drives and others that provide a change in the liquid level or a change in the operating mode of the entire hydraulic system. That is why DGS is often called sensors-signaling devices and sensors-relays.
On modern automotive equipment, a wide variety of sensors-hydraulic alarms are used - they should be described in more detail.
Types and characteristics of hydraulic alarm sensors
Today's sensors are divided into several types according to the physical principle of operation, the working environment (type of liquid) and its characteristics, the normal position of the contacts, the connection method and electrical characteristics.
According to the physical principle of operation, automotive DGS are divided into two groups:
● conductometric;
● Float.
Conductometric sensors are designed to work with electrically conductive liquids (mainly water and coolants). These DGS measure the electrical resistance between the signal and common (ground) electrodes, and when the resistance drops sharply, it sends a signal to an indicator or actuator. A conductivity sensor consists of a metal probe (usually made of stainless steel) and an electronic circuit (it includes a pulse generator and a signal amplifier). The probe performs the functions of the first electrode, the functions of the second electrode are assigned to the container itself with the liquid (if it is metal) or a metal strip laid along the bottom or walls of the container. The conductometric sensor works simply: when the liquid level is below the probe, the electrical resistance tends to infinity - there is no signal at the output of the sensor, or there is a signal about a low liquid level; When the liquid reaches the sensor probe, the resistance drops sharply (the liquid conducts current) - at the output of the sensor, the signal changes to the opposite.
Float sensors can work with any type of liquid, both conductive and non-conductive. The basis of such a sensor is a float of a particular design associated with a contact group. The sensor is located at the limit level that the liquid can reach during normal operation of the system, and when the liquid reaches this level, it sends a signal to the indicator or actuator.
There are two main types of float sensors:
● With a float connected to the movable contact of the contact group;
● With magnetic float and reed switch.
DGS of the first type are the simplest in design: they are based on a float in the form of a plastic probe or a hollow brass cylinder connected to the movable contact of the contact group. When the liquid level rises, the float rises and at a certain point there is a short circuit or, conversely, opening of the contacts.
Sensors of the second type have a slightly more complex design: they are based on a hollow rod with a reed switch (magnetic switch) located inside, along the axis of which an annular float with a permanent magnet can move. A change in the liquid level causes the float to move along the axis, and when the magnet passes by the reed switch, its contacts are closed or opened.
According to the type of working environment, automotive sensors-hydraulic alarms are divided into four main types:
● For work in water;
● For work in antifreeze;
● For work in oil;
● For operation in fuel (gasoline or diesel).
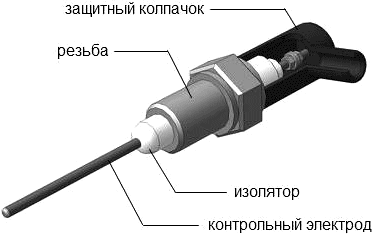
Sensor-hydraulic detector with a metal probe
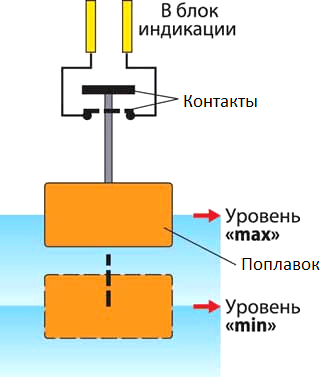
Diagram of a float sensor with a movable contact
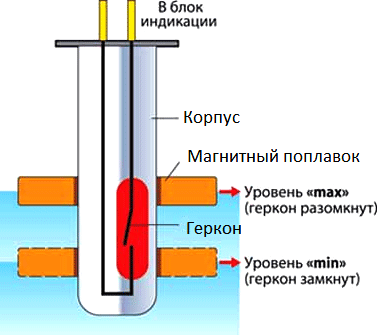
Diagram of a reed sensor with a magnetic float
DGS for different media differ in the materials used, and float sensors also differ in the size of the floats to provide sufficient lift in environments of different densities.
According to the normal position of the contacts, the sensors are divided into two groups:
● With normally open contacts;
● With normally closed contacts.
Sensors can have different ways of connecting to the electrical system: remote connectors with knife contacts, integrated connectors with knife contacts and integrated bayonet-type connectors. Typically, automotive DGS have four pins: two for power supply ("plus" and "minus"), one signal and one calibration.
Of the main characteristics of the sensors, it is necessary to highlight the supply voltage (12 or 24 V), the response delay time (from instantaneous operation to a delay of a few seconds), the operating temperature range, the current consumption, the mounting thread and the size of the turnkey hexagon.
Design and features of automotive sensors-hydraulic signaling devices
All modern automotive DGS have essentially the same design. They are based on a brass case, on the outside of which there is a thread and a turnkey hexagon. Inside the case there is a sensing element (float probe or steel probe), a contact group and a board with an amplifier / generator circuit. At the top of the sensor is an electrical connector or a wiring harness with a connector at the end.
The sensor is mounted in a tank or other element of the hydraulic system using a thread through an O-ring (gasket). With the help of a connector, the sensor is connected to the vehicle's electrical system.
A vehicle can have up to five or more sensors-hydraulic alarms that perform the functions of monitoring the level of fuel, coolant, oil in the engine, fluid in the hydraulic system, fluid in the power steering, etc.
How to choose and replace the sensor-hydraulic alarm
Liquid level sensors are important for the normal functioning of individual systems and the vehicle as a whole. Various signs indicate the breakdown of the DGS - false alarms of indicators or actuators (turning on or off pumps, etc.), or, conversely, the absence of a signal on the indicator or actuators. To avoid serious malfunctions, the sensor should be replaced as soon as possible.
For replacement, it is necessary to take sensors only of those types and models that are recommended by the automaker. DGS must have certain dimensions and electrical characteristics, when installing a sensor of another type, the system may malfunction. The sensor is replaced according to the vehicle's repair instructions. Usually, this work comes down to disabling the sensor, turning it out with a key, and installing a new sensor. Be sure to clean the installation site of the sensor from dirt, and use an O-ring (usually included) during installation. In some cases, it may be necessary to drain the liquid from the device.
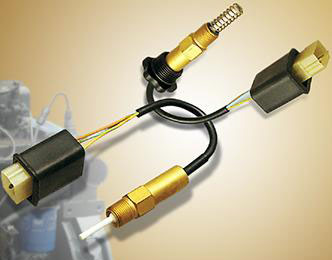
Sensors-hydraulic alarms
After installation, some sensors require calibration, the process of which is described in the relevant instructions.
With the correct selection and replacement of the sensor-hydraulic alarm, any system associated with it will function normally, ensuring reliable and safe operation of the vehicle.
Post time: Jul-12-2023