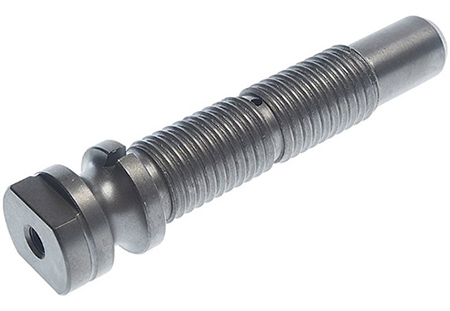
Installation of springs on the frame of the vehicle is carried out with the help of supports built on special parts - fingers. Everything about the fingers of the springs, their existing types, design and features of work in the suspension, as well as the correct choice of fingers and their replacement, you can find out in the presented article.
What is a finger spring?
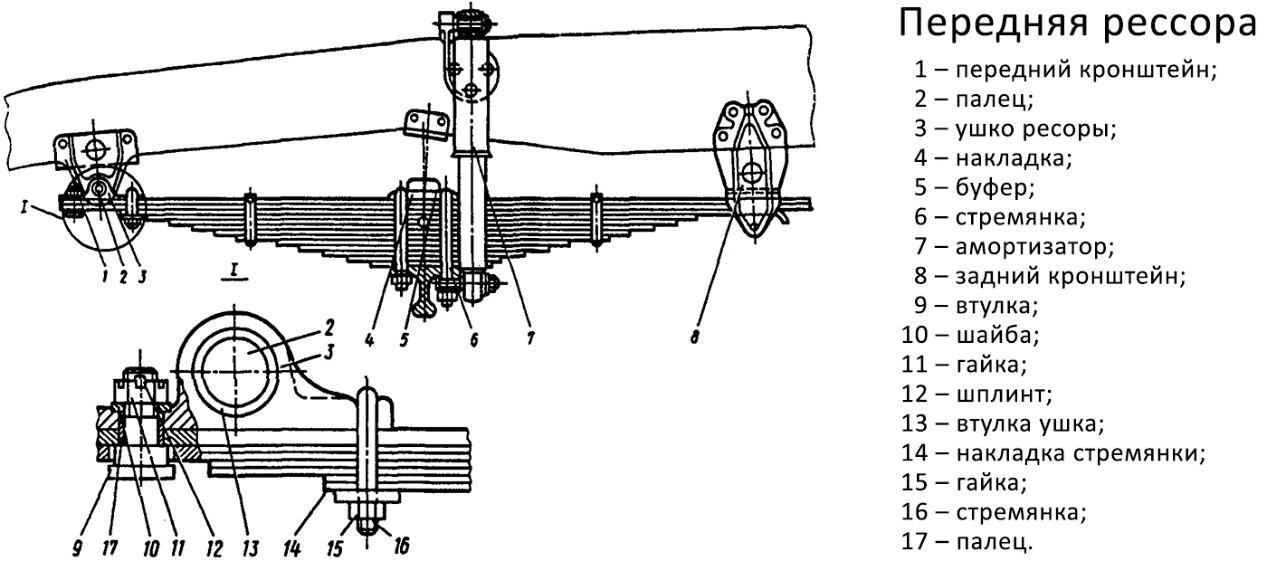
Spring suspension and the place of fingers in it
The finger of the spring is a common name for parts in the form of rods with various mounting methods (threaded, wedge, pin), protruding as axles or fasteners in the spring suspensions of vehicles.
The spring suspension, invented in the XVIII century, still remains relevant and is widely used in road transport. Springs act as elastic elements, which, due to their springy properties, smooth out shocks and tremors when the car moves along the unevenness of the road. The most common are semi-elliptical springs with two points of support on the frame - articulated and sliding. The articulated point provides the ability to rotate the spring relative to the frame, and the sliding point provides changes in the length of the spring during deformations that occur at the moments of overcoming unevenness of the road surface. The axis of the articulated support, which is located in the front of the spring, is a special element - the finger of the spring ear (or the finger of the front end of the spring). Rear sliding spring supports are most often made on bolts and other parts, but sometimes fingers of various designs are used in them.
Spring fingers are important suspension parts that constantly work under high loads (even when the car is not moving), so they are subject to intense wear and periodically require replacement. But before buying new fingers, you should understand the design and features of these parts.
Types, design and features of finger springs
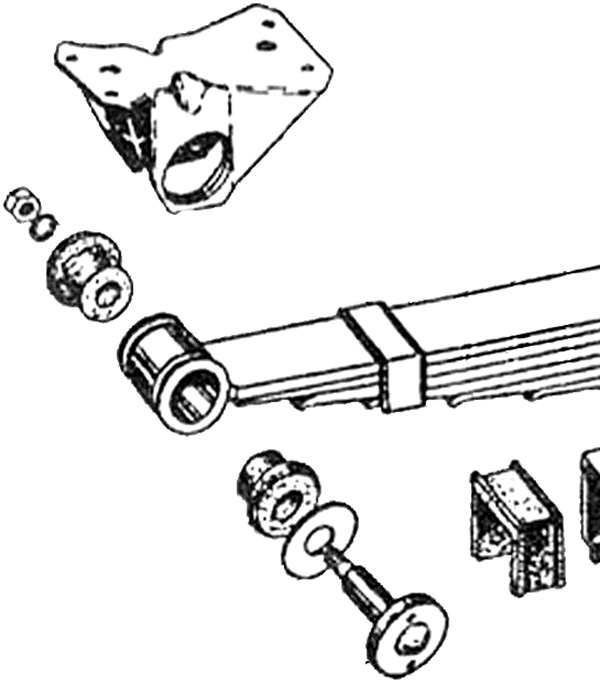
Installing the spring finger on the nut
The fingers of the springs are classified by the functions performed in the suspension (and, accordingly, by the place of installation), and by the method of installation.
According to the purpose (functions), the fingers are divided into three main groups:
● Fingers of the ear (front end) of the spring;
● Fingers of the rear support of the spring;
● Different mounting fingers.
In almost all leaf spring suspensions there is an ear finger, which is the main element of the front hinge fulcrum of the front and rear springs. This finger performs several functions:
● Acts as the axis (kingpin) of the articulated fulcrum;
● Provides a mechanical connection of the spring ear with the bracket located on the frame;
● Provides the transfer of forces and torques from the wheel to the frame of the vehicle.
Rear support pins can not be found in all spring suspensions, often this part is replaced by bolts or brackets without any threaded fasteners. These fingers can be divided into two main types:
● Single fingers fixed in the rear brackets of the spring (more precisely, in the inserts of the bracket);
● Double fingers gathered in an earring.
The most commonly used single fingers are located in the rear bracket, the spring rests on this finger (directly or through a special rigid gasket). Dual fingers are used much less often, and usually on cars of small mass (for example, on some UAZ models). The fingers are gathered in pairs with the help of two plates (cheeks), forming an earring for hanging the spring: the upper finger of the earring is installed in a bracket on the frame, the lower finger - in the ear on the back of the spring. This mount allows the rear end of the spring to shift in the horizontal and vertical planes when the wheel moves along uneven roads.
Various kinds of mounting pins are used to connect a package of spring plates to an ear (or leaf plate, at the end of which a loop is formed). Both fingers and bolts can be used for the connection in combination with various plastic and rubber bushings.
According to the method of installation, the fingers of the springs are divided into three types:
1. With fixation with transverse bolts of small diameter (jamming);
2. With nut fixation;
3. With pin fixation.
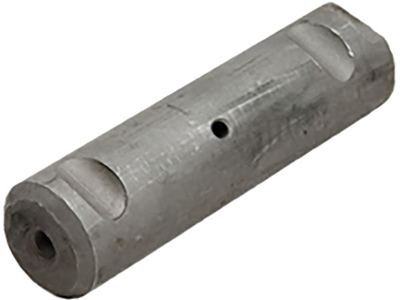
Finger ear springs with fixation with two bolts
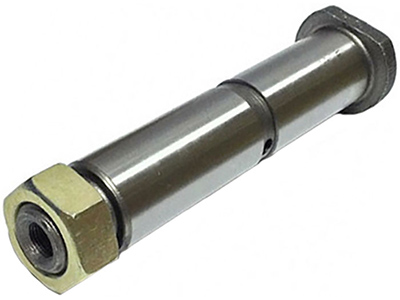
Finger ear springs with fixation with nut
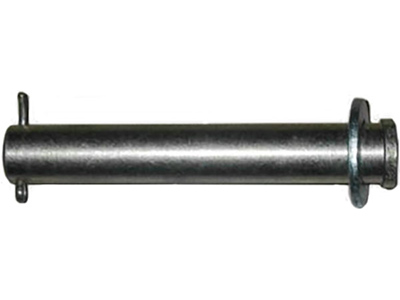
Finger of the rear support of the spring on the pin
In the first case, a cylindrical finger is used, on the lateral surface of which two transverse semicircular notches are made. The bracket has two transverse bolts that enter the notches of the finger, ensuring its jamming. With this installation, the finger is securely held in the bracket, it does not rotate around the axis and is protected from falling out under the influence of shock loads and vibrations. Fingers of this type are widely used in trucks, including domestic KAMAZ trucks.
In the second case, a thread is cut at the end of the finger, on which one or two nuts with thrust washers are screwed. Both conventional nuts and crown nuts can be used complete with a pin that is installed in the transverse hole in the finger, and reliably counters the nut.
In the third case, fingers are used, fixed only with a pin, which acts as a stop that prevents the part from falling out of the bracket. Additionally, a thrust washer is used with the pin.
Fingers of the first and second types are used in the front supports of the springs, the fingers of the third type - in the rear supports of the springs.
In a separate group, you can take out the fingers used in the earrings of the springs. In one cheek, the fingers are pressed, for which an extension with a longitudinal notch is performed under their heads - the finger is installed in the hole in the cheek with this extension, and is rigidly fixed in it. The connection with the second cheek is carried out by ordinary nuts or crown nuts with pins. As a result, a split connection is created, thanks to which the earring can be easily mounted and dismantled, and if necessary, disassembled to replace one finger.
Installation of the fingers of the front supports in the brackets is carried out through a solid or composite sleeve. In trucks, solid steel bushings are most often used, in which the fingers are installed through two ring rubber seals (cuffs). In lighter cars, composite bushings consisting of two rubber bushings with shoulders connected by external and internal steel bushings are widely used - this design is a rubber-metal hinge (silent block), which reduces the overall level of vibrations and noise of the suspension.
For the normal operation of the finger of the front support (spring ear), its lubrication is necessary - for this purpose, an L-shaped channel is performed in the fingers (drilling at the end and in the side part), and a standard oiler press is mounted in the end on the thread. Through the oiler, a grease is pumped into the channel of the finger, which enters the bushing and, due to pressure and heating, is distributed throughout the gap between the bushing and the finger. For an even distribution of lubricant (as well as for the correct installation of the part in the bracket), longitudinal and transverse notches of various shapes can be performed in the finger.
How to pick up and replace the finger springs
During the operation of the vehicle, all the fingers of the springs are subjected to significant mechanical loads, as well as the effects of negative environmental factors, which leads to their intensive wear, deformation and corrosion. Check the condition of the fingers and their bushings should be at each TO-1, during the inspection it is necessary to visually and instrumentally assess the wear of the fingers and bushings, and, if it is greater than permissible, change these parts.
Only those fingers and associated parts that are recommended by the vehicle manufacturer should be taken for replacement. The use of other types of parts can lead to premature wear and breakage of the suspension, a negative result can also have the independent manufacture of fingers (especially if the steel grade is incorrectly selected). You need to change the finger of the spring in accordance with the instructions for the repair and maintenance of the vehicle. Usually this operation is carried out as follows:
1. Hang a part of the car from the side of the spring to be repaired, unload the spring;
2. Disconnect the shock absorber from the spring;
3. Release the finger - unscrew the nut, unscrew the bolts, remove the pin or perform other operations in accordance with the type of attachment of the finger;
4. Remove the finger - knock it out or pull it out of the sleeve with a special device;
5. Inspect the bushing and, if necessary, remove it;
6. Install new parts, having previously performed lubrication;
7. Reverse build.
It should be noted that in some cases, you can remove the finger only with the help of special pullers - this device must be taken care of in advance. The puller can be purchased or made independently, although factory products work much more efficiently.
After replacing the finger, it is necessary to fill it with grease through a press oiler, in the future to perform this operation with appropriate maintenance.
If the finger of the spring is selected and replaced correctly, the suspension of the car will reliably serve in all conditions, providing comfortable and safe movement.
Post time: May-06-2023