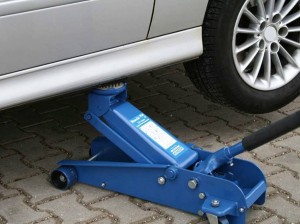
A car jack is a special mechanism that allows you to carry out routine repairs of a truck or car in cases where this repair must be carried out without supporting the car on wheels, as well as changing wheels directly at the site of a breakdown or stop. The convenience of a modern jack is in its mobility, low weight, reliability and ease of maintenance.
Most often, jacks are used by drivers of cars and trucks, motor transport enterprises (especially their mobile teams), car services and tire fitting.
Main features
Load capacity (denoted in kilograms or tons) is the maximum weight of the load that the jack can lift. To determine whether the jack is suitable for lifting this car, it is necessary that its carrying capacity is not lower than that of a standard jack or be at least 1/2 of the gross weight of the car.
The support platform is the lower support part of the jack. It is usually larger than the upper bearing part to provide as little specific pressure on the bearing surface as possible, and is provided with "spike" protrusions to prevent the jack from sliding on the support platform.
Pickup is a part of the jack designed to rest in a car or a lifted load. On screw or rack jacks for old models of domestic cars, it is a folding rod, on others, as a rule, a rigidly fixed bracket (lifting heel).
Minimum (initial) pick-up height (Nmin) - the smallest vertical distance from the support platform (road) to the pickup in its lower working position. The initial height must be small in order for the jack to enter between the support platform and the suspension or body elements.
Maximum lifting height (N.max) - the greatest vertical distance from the support platform to the pick-up when lifting the load to full height. An insufficient value of Hmax will not allow the jack to be used to lift vehicles or trailers where the jack is at a high altitude. In case of lack of height, spacer cushions can be used.
Maximum jack stroke (L.max) - the greatest vertical movement of the pickup from the lower to the upper position. If the working stroke is insufficient, the jack may not "tear" the wheel off the road.
There are several types of jacks, which are classified according to the type of construction:
1.Screw jacks
2.Rack and pinion jacks
3.Hydraulic jacks
4.Pneumatic jacks
1. Screw jacks
There are two types of screw car jacks - telescopic and rhombic. Screw jacks are popular with motorists. At the same time, rhombic jacks, the carrying capacity of which varies from 0.5 tons to 3 tons, are most popular with car owners and are often included in the set of standard road tools. Telescopic jacks with a carrying capacity of up to 15 tons are indispensable for SUV and LCV vehicles of various types.
The main part of the screw jack is a screw with a hinged load-bearing cup, driven by a handle. The role of load-bearing elements is performed by a steel body and a screw. Depending on the direction of rotation of the handle, the screw raises or lowers the pick-up platform. Holding the load in the desired position occurs due to the braking of the screw, which ensures the safety of work. For horizontal movement of the load, a jack on a sled equipped with a screw is used. The load capacity of screw jacks can reach 15 tons.
The main advantages of screw jacks:
● significant working stroke and lifting height;
● light weight;
● Low price.
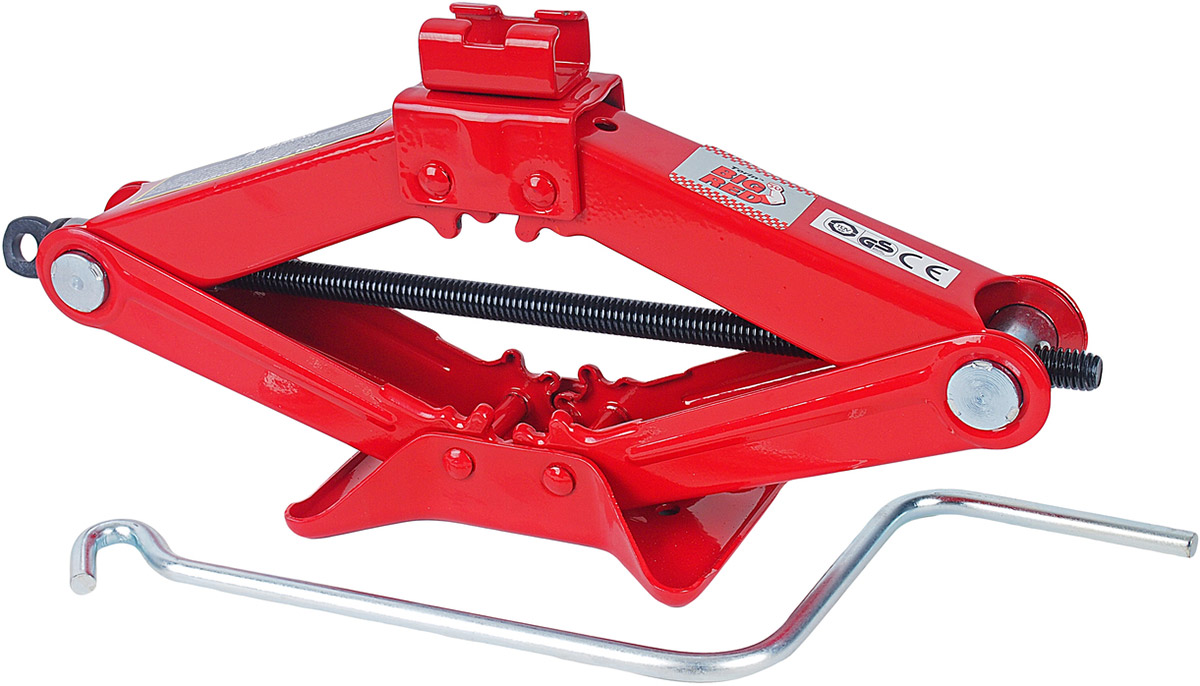
Screw jacks
The screw jack is reliable in operation. This is due to the fact that the load is fixed by a trapezoidal thread, and when lifting the load, the nut rotates idle. In addition, the advantages of these tools include strength and stability, as well as the fact that they can work without additional stands.
2. Rack and pinion jacks
The main part of the rack jack is a load-carrying steel rail with a support cup for the load. An important feature of the rack jack is the low location of the lifting platform. The lower end of the rail (paw) has a right angle for lifting loads with a low support surface. The load lifted on the rail is held by locking devices.
2.1. Lever
The rack is extended by a swinging drive lever.
2.2. Toothed
In gear jacks, the drive lever is replaced by a gear, which rotates through a gearbox using a drive handle. In order for the load to be securely fixed at a certain height and in the desired position, one of the gears is equipped with a locking mechanism - a ratchet with a "pawl".
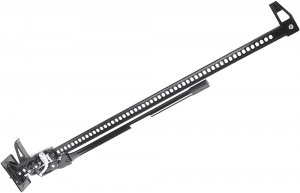
Rack and pinion jacks
Rack jacks with a carrying capacity of up to 6 tons have a single-stage gearbox, from 6 to 15 tons - two-stage, over 15 tons - three-stage.
Such jacks can be used both vertically and horizontally, they are easy to use, well repaired and are a universal tool for lifting and fixing cargo.
3. Hydraulic jacks
Hydraulic jacks, as the name suggests, work by pressurizing fluids. The main load-bearing elements are the body, the retractable piston (plunger) and the working fluid (usually hydraulic oil). The housing can be both a guide cylinder for the piston and a reservoir for the working fluid. The reinforcement from the drive handle is transmitted through the lever to the discharge pump. When moving upwards, the liquid from the reservoir is fed into the cavity of the pump, and when pressed, it is pumped into the cavity of the working cylinder, extending the plunger. The reverse flow of the liquid is prevented by the suction and discharge valves.
To lower the load, the shut-off needle of the bypass valve is opened, and the working fluid is forced out of the cavity of the working cylinder back into the tank.
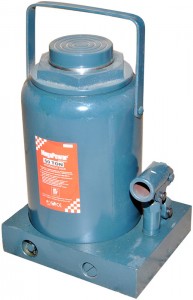
Hydraulic jacks
The advantages of hydraulic jacks include:
● high load capacity - from 2 to 200 tons;
● structural rigidity;
● stability;
● smoothness;
● compactness;
● small force on the drive handle;
● high efficiency (75-80%).
The disadvantages include:
● small lifting height in one working cycle;
● complexity of the design;
● it is not possible to adjust the lowering height precisely;
● Such jacks can cause significantly more serious breakdowns than mechanical lifting devices. Therefore, they are more difficult to repair.
There are several types of hydraulic jacks.
3.1. Classic bottle jacks
One of the most versatile and convenient types is a single-rod (or single-plunger) bottle jack. Often, such jacks are part of the standard road tools of trucks of various classes, from light-tonnage commercial vehicles to large-tonnage road trains, as well as road construction equipment. Such a jack can even be used as a power unit for presses, pipe benders, pipe cutters, etc.
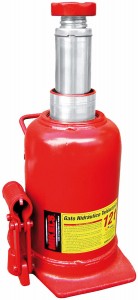
Telescopic
jacks
3.2. Telescopic (or double-plunger) jacks
It differs from single-rod only by the presence of a telescopic rod. Such jacks allow you to lift the load to a great height, or reduce the pickup height, while maintaining the maximum lifting height.
They have a carrying capacity of 2 to 100 tons or more. The housing is both a guide cylinder for the plunger and a reservoir for the working fluid. The lifting heel for jacks with a carrying capacity of up to 20 tons is located at the top of the screw screwed into the plunger. This allows, if necessary, by unscrewing the screw, to increase the initial height of the jack.
There are designs of hydraulic jacks, where an electric motor connected to the vehicle's on-board network, or a pneumatic drive, is used to drive the pump.
When choosing a hydraulic bottle jack, it is necessary to take into account not only its carrying capacity, but also the pick-up and lifting heights, since the working stroke with sufficient carrying capacity may not be enough to lift the car.
Hydraulic jacks require monitoring of the fluid level, condition and tightness of the oil seals.
With infrequent use of such jacks, it is recommended not to tighten the locking mechanism to the end during storage. Their work is possible only in an upright position and only (like any hydraulic jacks) for lifting, and not for long-term holding of the load.
3.3. Rolling jacks
Rolling jacks are a low body on wheels, from which a lever with a lifting heel is lifted by a hydraulic cylinder. The convenience of work is facilitated by removable platforms that change the height of picking up and lifting. It should not be forgotten that a flat and hard surface is required to work with a rolling jack. Therefore, this type of jacks, as a rule, is used in car services and tire shops. The most common are jacks with a carrying capacity of 2 to 5 tons.
4. Pneumatic jacks
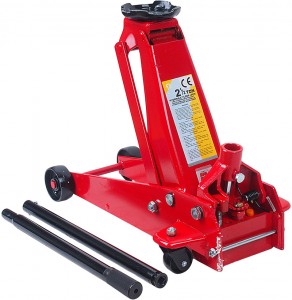
Rolling jacks
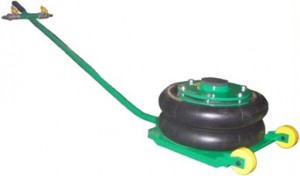
Pneumatic jacks
Pneumatic jacks are indispensable in the case of a small gap between the support and the load, with small movements, precise installation, if work is to be done on loose, uneven or swampy ground.
The pneumatic jack is a flat rubber-cord sheath made of a special reinforced fabric, which increases in height when compressed air (gas) is supplied to it.
The carrying capacity of the pneumatic jack is determined by the working pressure in the pneumatic drive. Pneumatic jacks come in several sizes and different load capacities, usually 3 – 4 – 5 tons.
The main disadvantage of pneumatic jacks is their high cost. It is influenced by the relative complexity of the design, mainly associated with the sealing of joints, the expensive technology for the manufacture of sealed shells and, finally, small industrial batches of production.
Key characteristics when choosing a jack:
1.Carrying capacity is the maximum possible weight of the load to be lifted.
2.The initial pick-up height is the smallest possible vertical distance between the bearing surface and the support point of the mechanism in the lower working position.
3.The lifting height is the maximum distance from the supporting surface to the maximum operating point, it should allow you to easily remove any wheel.
4.The pick-up is the part of the mechanism that is designed to rest on the object being lifted. Many rack and pinion jacks have a pick-up made in the form of a folding rod (this method of fastening is not suitable for all cars, which limits its scope), while the pick-up of hydraulic, rhombic and other models is made in the form of a rigidly fixed bracket (lifting heel).
5.Working stroke - moving the pickup vertically from the lower to the upper position.
6.The weight of the jack.
Safety rules when working with jacks
When working with jacks, it is necessary to follow the basic safety rules when working with jacks.
When replacing the wheel and during the repair work with lifting and hanging the car, it is required:
● fix the wheels on the opposite side of the jack in both directions to avoid the car rolling back and falling off the jack or stand. To do this, you can use special shoes;
● After raising the body to the required height, regardless of the design of the jack, install a reliable stand under the load-bearing elements of the body (sills, spars, frame, etc.). It is strictly forbidden to work under the car if it is only on the jack!
Post time: Jul-12-2023